In today’s rubber processing industry, the choice of equipment is crucial for improving production efficiency, product quality, and cost control. As a leading manufacturer of rubber kneaders, Crowns Machinery understands the pivotal role that rubber kneaders play in this field. This article explores the key advantages of using rubber kneaders and explains how these benefits help businesses thrive in a competitive market.
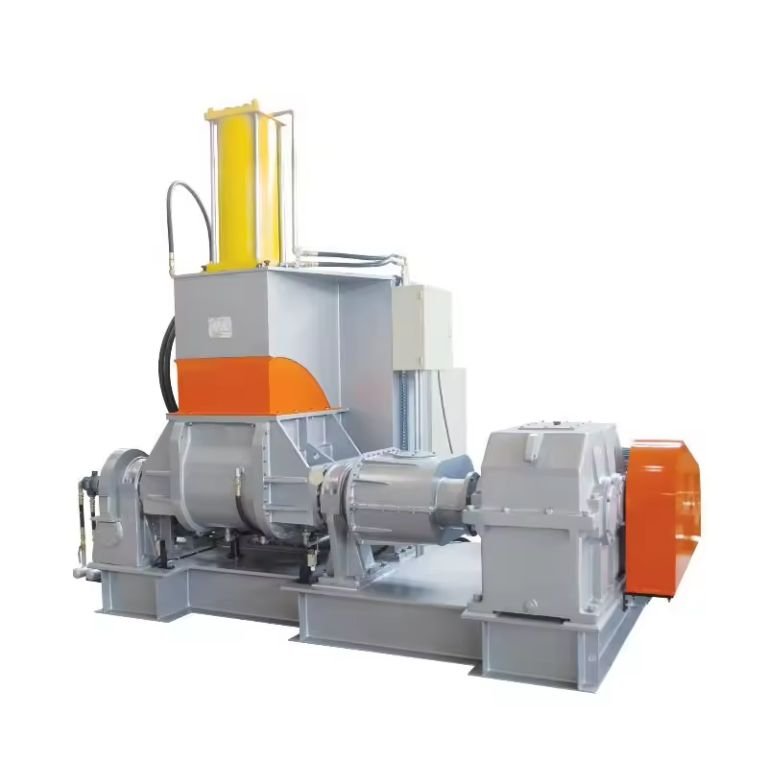
Table of Contents
Improved Mixing Efficiency
Rubber kneaders are designed to ensure materials are thoroughly and evenly dispersed during the mixing process. Whether mixing natural or synthetic rubber with additives like fillers, plasticizers, or vulcanizing agents, rubber kneaders excel at efficient mixing. The rotor design is critical, utilizing powerful shearing and kneading actions to fully integrate materials, reducing processing time and enhancing the consistency of the mixture.
Compared to traditional mixing methods, rubber kneaders complete the mixing process in a shorter time, significantly boosting production efficiency. This is especially beneficial for large-scale production, as more batches can be completed in less time, greatly increasing output. The uniformity of the mix directly impacts the final product’s performance, making it more competitive in the market.
Rubber kneaders also handle high-viscosity, high-filler rubber materials that are difficult to mix evenly with traditional equipment. The powerful shearing and kneading actions of the kneader break down agglomerates, ensuring uniformity. This efficient mixing not only speeds up production but also reduces material waste, further lowering production costs.
Increased Productivity
Rubber kneaders are equipped with advanced automation control systems that minimize the need for manual intervention. These systems precisely control the kneading cycle’s time, temperature, and pressure, allowing faster completion of each batch, thus significantly boosting productivity. Automation also reduces errors from manual operations, ensuring consistent and stable production processes.
In producing high-performance rubber products like tires, seals, and conveyor belts, maintaining consistent product quality is critical. Rubber kneaders precisely control each kneading process, ensuring every batch meets the same quality standards. For companies producing various products with different specifications, the flexibility of rubber kneaders is particularly valuable. They can quickly adjust kneading parameters to meet changing market demands.
Moreover, the automated control systems enable remote monitoring and diagnostics, allowing operators to monitor production status in real time and make necessary adjustments. This not only enhances production efficiency but also reduces the complexity and cost of equipment maintenance.
Energy Savings and Cost Efficiency
With rising energy costs, companies increasingly prioritize energy-efficient equipment. Crowns Machinery’s rubber kneaders use energy-saving motors and optimized rotor designs, ensuring efficient mixing while minimizing energy consumption. Precise temperature and pressure control prevent unnecessary energy waste, leading to lower production costs.
This energy-efficient design helps companies reduce the production cost per unit and maintain price competitiveness in the market. Additionally, the energy-saving features align with current sustainability trends, helping companies achieve green production goals. This energy efficiency not only lowers operating costs but also positively impacts long-term sustainability.
The high production efficiency of rubber kneaders significantly reduces labor costs. Automation reduces dependence on skilled labor while ensuring high-quality production output. Companies can allocate the saved labor resources to value-added activities like R&D and marketing, further enhancing competitiveness.
Versatility and Broad Applicability
Rubber kneaders are versatile, handling various types of rubber and additives, making them suitable for a wide range of industrial applications. They are essential not only in tire manufacturing and seal production but also in aerospace, construction, medical, and other fields. For example, in medical device manufacturing, rubber kneaders process high-purity rubber materials, ensuring products meet stringent hygiene standards.
In the rubber compounding industry, rubber kneaders effectively mix various material combinations, ensuring uniformity and stability in the final product. This is crucial for producing high-quality composite materials, such as heat-resistant and wear-resistant rubber parts used in the automotive industry. This versatility allows companies to respond flexibly to diverse market demands and offers opportunities to expand into multiple sectors.
Rubber kneaders can also process new and environmentally friendly materials, which is increasingly important in today’s eco-conscious market. Companies can use advanced rubber kneaders to develop and produce eco-friendly products, gaining a competitive edge.
Consistency in Product Quality
Consistency in product quality is a key measure of production success. Rubber kneaders, with their precise temperature and pressure control, ensure each batch meets expected quality standards. This capability is especially important for producing high-performance rubber products like industrial seals and highly wear-resistant tires.
The efficient mixing process of rubber kneaders reduces the rate of defective products, improving production efficiency and reducing material waste, further enhancing the economic efficiency of the production line. Companies can produce higher-quality products with greater consistency, earning customer trust and market recognition.
Conclusion
Rubber kneaders offer significant advantages in improving mixing efficiency, productivity, energy savings, cost-effectiveness, versatility, and product quality consistency. As a leading manufacturer, Crowns Machinery is committed to providing the most advanced rubber kneaders to help clients stay ahead in a competitive market. By adopting our rubber kneaders, companies can optimize their production processes, significantly reduce operating costs, and enhance product quality, leading to market success.