Rubber Extruder
Home » Rubber Extruder
Crowns Machinery’s rubber extruder are industry leaders for superior craftsmanship and quality. Innovative design and reliability combine to bring superior performance to your production line.
Rubber Extruder For Sale
Rubber extruders are essential in mixing and processing rubber. They are used to make many rubber products. Our rubber extruder has several key parts. Each is designed for top performance and durability:
Head (Extrusion Die Head): It shapes the extruded material into forms. These include tire inner tubes, tire treads, and semi-finished products. The die head can be customized to meet specific product requirements.
Screw: Our screws are made of high-strength alloy steel. They are designed to resist wear and corrosion. This ensures long-lasting performance and efficient material processing.
Barrel: The barrel houses the screw. It is made from durable materials to keep high pressure and temperature during extrusion.
Fixed Beat Device: Ensures consistent feeding and maintains the stability of the material flow.
Haul-off Device: Pulls the extruded material out of the die head, ensuring smooth and uniform extrusion.
Cutting Device: Precisely cuts the extruded material into desired lengths, suitable for various applications.
Dosing Device: Controls the amount of raw material fed into the extruder, allowing for precise material usage and reducing waste.
Transmission Device: Powers the screw and other moving parts of the extruder, designed for efficient energy use.
Control System: An advanced PLC control system allows precise control of the extrusion process. It controls temperature, pressure, and screw speed.
As a professional rubber extruder manufacturer, Crowns Machinery possesses strong beliefs in both product quality control and after-sales service, which is why it is highly appreciated by customers from all over the world.
No matter what your usage needs are, if you need any help, please feel free to contact us, we will provide you with the most reliable rubber extrusion equipment as well as competitive factory price.
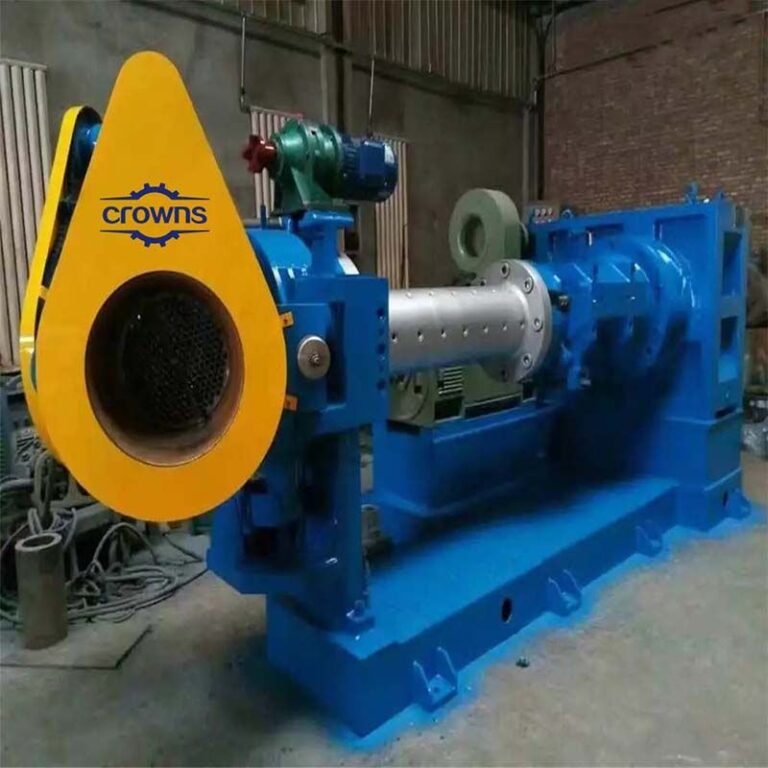
Parameters
Items | Diameter of Screw(mm) | L/D Ratio | Speed of Screw Max(r/min) | Driving Power(kw) | Maximum output (kg/h) | Weight(kg) |
---|---|---|---|---|---|---|
XJD-75 | 75 | 16 | 60 | 37 | 120 | 1200 |
XJD-90 | 90 | 16 | 55 | 55 | 300 | 3200 |
XJD-120 | 120 | 16 | 50 | 110 | 600 | 5200 |
XJD-150 | 150 | 16 | 45 | 135 | 900 | 6500 |
XJW-45 | 45 | 16 | 70 | 7.5 | 50 | 500 |
XJW-50 | 50 | 16 | 65 | 7.5 | 60 | 600 |
XJW-75 | 75 | 16 | 60 | 37 | 120 | 1200 |
XJW-90 | 90 | 16 | 55 | 55 | 300 | 3200 |
XJW-120 | 120 | 16 | 50 | 110 | 600 | 5200 |
XJW-150 | 150 | 16 | 45 | 135 | 720 | 6500 |
XJW-200 | 200 | 14 | 35 | 185 | 1500 | 8500 |
Working Principle
The working principle of a rubber extruder involves passing the raw material through a shaping die to extrude a rubber profile with a consistent cross-section design and continuous length. To make good rubber products, you must control temperature, pressure, and screw speed precisely.
Feeding: The extrusion process begins by loading the raw rubber material into the hopper. This material is typically in the form of rubber strips, granules, or sheets. Consistent and even feeding ensures smooth operation and high-quality output.
Heating: The rubber is preheated to the right temperature along the extruder. This is done with electric or steam heating. It makes the rubber soft and elastic. Precise temperature control is crucial. It helps achieve the desired material properties and prevent degradation.
Screw Conveyor: In the extruder, a rotating screw moves the rubber forward. It mixes the rubber thoroughly by pressure and shear. The screw’s speed and design are critical for achieving uniform mixing and preventing material defects.
Compression Shaping Die Head: Near the end of the extruder, the shaping die head forms the material into continuous profiles, sheets, and tubes. The die head’s size and shape can be customized to suit different product needs. The die head must be precisely engineered to ensure the final product’s shape and dimensions meet specifications.
Cooling and Vulcanization: After molding, the extruded rubber needs to be cooled and vulcanized. This process can involve air-cooling, water baths, or other cooling solutions. The choice depends on the specific shape and properties needed. Proper cooling and vulcanization are essential to stabilize the material and achieve the desired mechanical properties.
Cutting and Shaping: The final step involves cutting the rubber into specific lengths for further processing. This is done using knives, saws, or other cutting tools. Precise cutting makes sure the product meets the needed dimensions. It gets it ready for later manufacturing.
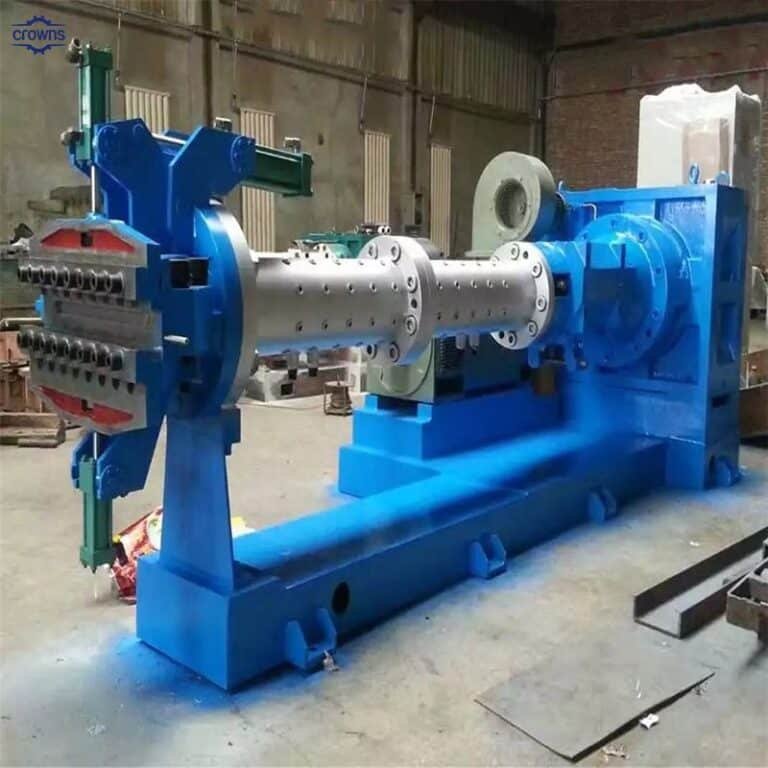
Advantages of Rubber Extruders
Rubber Extruders are key in the rubber industry. They are efficient, consistent, and versatile. They offer the following benefits in many industrial uses:
Quality Control: Rubber Extruders maintain consistency in product performance, leading to better quality control.
Consistency: Extruders make the final rubber product’s size and shape consistent. They cut waste and improve quality.
High productivity: Extruders can make rubber products continuously. They do so with high productivity, which makes them ideal for mass production.
Customization: Extruders can be flexibly customized to meet different production needs.
Energy efficient: Cold feed extruders process rubber at room temperature. Hot feed extruders require only a little heat to operate. This makes them very energy efficient.
Material compatibility: Rubber extruders can process all kinds of rubber, like natural, synthetic, and silicone. So, they can be used in many industries, such as automotive, construction, and medical.
Mixing capacity: Rubber extruders, especially twin-screw ones, mix well. They ensure even dispersion of fillers, colorants, and other rubber compounds.
Precision: Rubber extruders allow precise control of extrusion. This control results in very accurate tolerances in the final product.
Reduced labor costs: Automated production is effective. It replaces manual work and cuts labor costs. It also improves production safety.
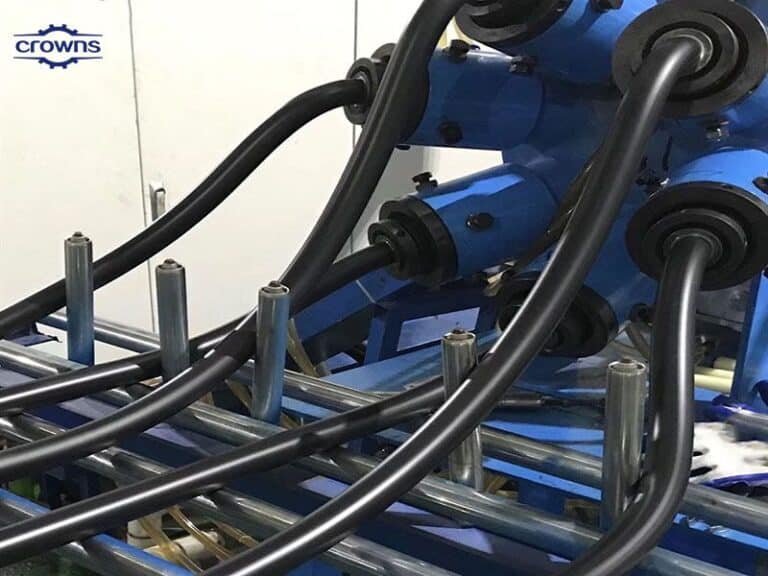
applications
Rubber extruders make rubber and plastic products by extrusion. They can shape rubber mixtures into tubes, plates, strips, pellets, and tire treads. They are also used to plasticize, mix, and refine rubber and plastics. They are also used to compound rubber and synthetic rubber.
Tyre manufacturing: rubber extruders are best known for their use in tire production, such as tire treads and sidewalls.
Hoses and tubes: Rubber extruders are common. They make hoses and tubes for many industrial uses. These include medical, automotive, and hydraulic hoses.
Seals and Gaskets: Rubber extruders make seals and gaskets. They are used in industries like automotive, construction, and manufacturing. The seals and gaskets prevent leaks and provide insulation.
Wire & Cable Insulation: Rubber Extruders are also commonly used to manufacture insulation for telecoms and power cables.
Conveyor belts: Rubber extruders make conveyor belts. They are used in manufacturing, logistics, and material handling.
Moldings and profiles: Rubber extruders make rubber profiles and moldings for many uses. These include making car windscreens, seals for doors and windows, and building expansion joints.
Automotive, aircraft, and aerospace components: Rubber extruders are used to make many car parts. These include window seals, gaskets, rubber bushings, and door profiles.
Sports equipment: Rubber extruders make many sports equipment parts. These include tennis racket handles, grips, and golf clubs.
Food processing: Rubber extruders can meet food safety requirements. They can be used for food-grade production. They make seals, gaskets, and conveyor belts. These products follow food safety rules.
Medical equipment: Rubber extruders make medical equipment parts. These include seals and tubes.
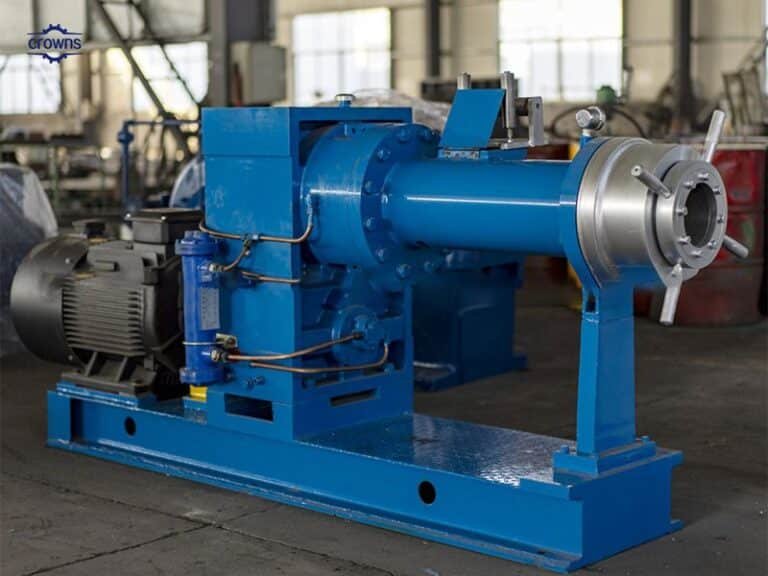
Supply Advantages of Crowns Machinery
Excellent product quality: Our machines have been getting good market feedback and recognition from many countries. We are working hard to meet the high-quality needs of our customers. We always believe that quality is our enterprise’s life.
Price Discounts: Our prices are low and competitive compared to the temporarily high profits. We look forward to long-term cooperation with customers. We also offer good discounts for large orders.
Timely Delivery: Crowns Machinery has a full production management and planning system. It ensures that all tasks are done in order. This will guarantee that orders are delivered on time and in full. It will also help our partners follow their plans.
Perfect After-sales Service: We provide great after-sales services. They can quickly solve the problems our customers have when using our machines. This truly achieves worry-free after-sales service for our customers.
Strong Technical Support: We have advanced technology and a pro technical team. They can support our customers and provide solutions at any time.
Customization: Our machines can be customized to meet customer needs. Just tell us your demands, and we will make a solution for you.
Good Reputation: Crowns Machinery has had a great reputation in the rubber machinery industry for over 10 years. We built it with hard work on product quality. We always put quality and customers first. This focus has won the trust and long-term business of many new and old customers.
Strong Production Capacity: Crowns Machinery has the latest production equipment. It also has experienced workers and a big production line. Our strong processing capability can meet all kinds of large orders.
FAQ
Selecting the right machine requires thought about many factors. These include production needs, material properties, machine specs, and budget. First, determine the required production capacity and product specifications, such as the thickness and width of the rubber sheet. Next, select a machine that can handle the material being used, ensuring it has the right roll diameter and roll length. Finally, consider the machine’s durability and maintenance needs. Choose a supplier with good after-sales and technical support.
A good quality Rubber Extruder Machine will generally last for more than 10 years. Regular maintenance and servicing, like cleaning and lubrication, can greatly extend the service life. They also involve replacing parts.
Regularly inspect and clean the machine to ensure that there is no accumulation of dust and impurities. Regularly lubricating rollers and transmission parts. Also, timely replacing worn parts. This keeps the machine running well and extends its life.
The Rubber Extruder Machine is widely used in the rubber, chemical, electronics, automotive, and building materials industries. It is for making rubber sheets, seals, gaskets, and other products.
Continue reading:5 Daily Applications For Rubber Extruders
Pay attention to safety when operating and avoid fingers close to the drum. Regularly check the status of the machine to ensure proper operation. Follow the operation manual for standardized operation to prevent accidents.
We offer the following types of Rubber Extruder Machines to meet different production needs:
Cold Feed Rubber Extruder: Ideal for processing rubber compounds at ambient temperatures with significant energy savings.
Hot Feed Rubber Extruder: Requires preheating of the material and is suitable for rubber products with high-quality requirements, such as tire manufacturing.
Single Screw Rubber Extruder: Suitable for simple extrusion tasks.
Twin Screw Rubber Extruder: High mixing capacity, suitable for complex rubber compound processing.
Pin-type rubber extruder: suitable for demanding material mixing to ensure uniform distribution.
Thermoplastics: e.g., polyethylene, polypropylene, polyvinyl chloride, etc.
Thermosets: such as phenolic plastics, epoxy resins, etc.
Silicone: Commonly used in sealing and insulating applications.
Thermoplastic elastomers: such as polyurethane elastomers, are used in the production of rubber hoses, seals, and strips.
The main differences between Rubber Extruder and Plastic Extruder are the raw materials, the processing requirements, and the application areas.
Raw Materials: Our Rubber Extruder handles rubber. It works with natural and synthetic rubber. The Plastic Extruder handles a wide range of thermoplastics and thermosets.
Temperature Requirements: Rubber extruders need lower temperatures to avoid overheating and melting. Plastic extruders need higher temperatures to melt the plastic.
Design Features: Our Rubber Extruders have higher pressure and larger pressure transfer parts. Plastic Extruders have more heating capacity and precise temperature control.
Areas of Application: The Rubber Extruder is used for the production of rubber products such as seals, rubber hoses, and bands. The Plastic Extruder is used for the production of plastic pipes, films, profiles, and containers.
You can contact our sales team via our website, phone, or email and we will provide you with a detailed ordering process and quote. We are committed to providing you with the most suitable solution to meet your production needs.
Lead times depend on the specific order and type of machine and are typically weeks to months. Please contact us for details and we will arrange production and delivery as soon as possible according to your needs.
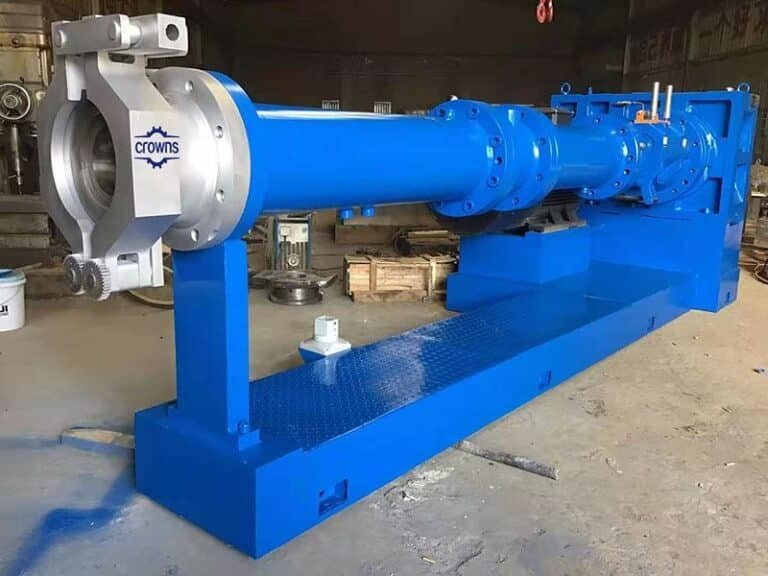
Menu
Get Quotes
- Engineer: Wiki Wang
- Email:sales@crownsmachine.com
- Whatsapp:+8618266230982