Choosing the right rubber calender is crucial for your business. This equipment choice directly affects productivity and product quality. A good rubber calender makes production stable and efficient. It raises output and cuts costs. Also, the right calender choice can keep the product consistent. It can cut the rate of defects due to equipment. In the following article, Crowns Machinery will take you through the process of selecting the right rubber calender.
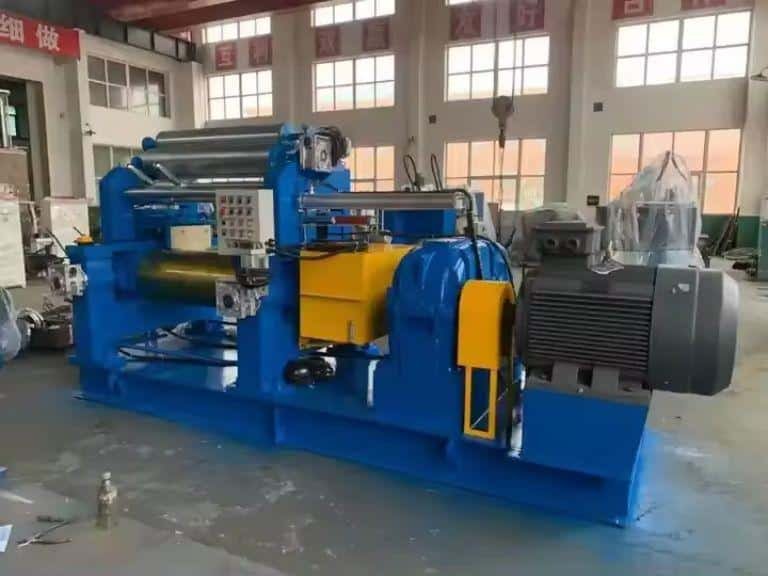
Table of Contents
Understanding Rubber Calender
A rubber calender is a machine used to press rubber into shapes and thicknesses. It is widely used in making rubber products like tires, conveyor belts, and waterproof materials.
A rubber calender puts rubber between its rollers. It shapes the rubber into a sheet or a specific shape with high heat and pressure. There are several subdivisions:
Type I Rubber Calender
Type I calenders are the most common type of calender and consist primarily of two to four horizontally aligned drums. This setup is simple. It is easy to use and maintain. It is good for making most regular rubber products, like tire treads and adhesive tapes. Due to its simple and compact structure, the I-type calender is usually used for small-batch production.
L-Type Rubber Calender
The L-type calender has an L-shaped arrangement of rollers, usually consisting of three rollers. This design can handle wider rubber and provide more calendering force. The L-shaped calender is widely used to make large or multi-layer materials like conveyor belts and waterproofing rolls. This model is for high production volumes and applications needing high calendering forces. This model is suitable for high output and production processes that require multi-layer calendering.
Z type rubber calender
The Z-type calender has a Z-shaped arrangement of rollers, also consisting of three rollers. This setup has the advantage of more flexibility and versatility. It allows different materials to be calendered at the same time into composites or in layers. The Z calender is widely used for complex calendering operations. It is used especially for making demanding specialty rubber products, such as aerospace materials, high-performance seals, and more.
Configurations and Uses
The selection and configuration of a rubber calender has a direct impact on productivity and product quality. By understanding the calenders’ types and where they are used, companies can choose the best equipment for their needs. This will improve productivity and ensure product quality.
The calendar’s configuration consists of options like the number of rollers, heating system, cooling system, and drive mode. These can be selected based on different production needs. Advanced calendering machines are usually equipped with automatic control systems, which can better improve production efficiency and product quality.
A rubber calendering machine is vital in the rubber products industry. It is used for tires and hoses in the auto industry, waterproofing rolls for construction, and gaskets for daily items. All these products depend on this machine.
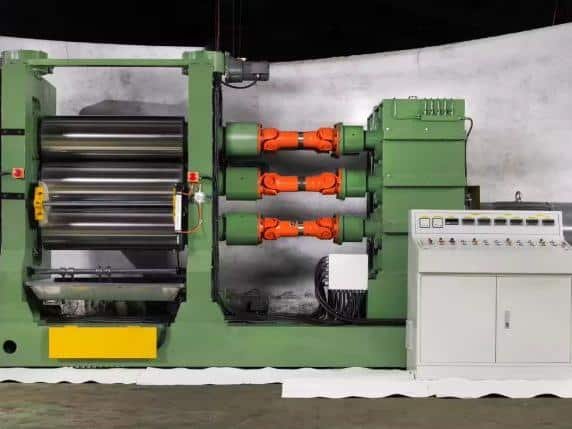
Factors to Consider When Choosing a Rubber Calender
Assessing business needs
Scale of production
Small-scale production: suitable for start-ups and may require smaller compact machines.
Large-scale production: suitable for high-volume standardized production, requiring large, efficient machines.
Product Type
Single-layer products: e.g. simple rubber sheets or tread materials, usually choose type I calenders.
Multi-layer composite products: For example, composite tapes or high-performance seals may need an L or Z calender. These are for complex production.
Machine Specifications
Roll Size: Find the largest and smallest roll sizes. This is to ensure the machine can handle the expected demand.
Motor Rating: The motor’s power directly affects the machine’s performance and efficiency. Higher power motors provide more calendering force, but this also means higher energy consumption.
Line Speed: Choose the appropriate line speed for your production needs. High-speed production lines are for mass production. But, they need stable rubber quality at high speeds.
Technical features
Nip Adjustment: Adjusting the nip affects product thickness and consistency. The ability and accuracy of the adjustment are key. Therefore, choosing a calender with precise nip adjustment function is important.
Automatic Lubrication System: An efficient lubrication system extends the life of the machine and reduces maintenance. Auto-lubrication can make equipment easier to use. It ensures that production continues.
Maintenance-friendly features: Maintenance-friendly structural design helps to reduce downtime and increase productivity. So, when choosing a calendar, consider if the structure is easy to take apart and clean. Also, see if the parts are easy to replace.
Cost Considerations
Initial cost: While the purchase cost of a machine is certainly an important factor, you can’t just look at the price. Quality and performance are equally important. A high-quality machine boosts productivity and has fewer breakdowns.
Long-term operating costs
Maintenance costs: include the cost of regular maintenance and unexpected repairs. Choosing a machine with high durability and low maintenance needs can reduce long-term operating costs.
Parts Replacement: Imported equipment may need costly imported parts. Domestic equipment may have an advantage in part availability and price.
Energy Costs: Energy-efficient equipment can lead to big savings in electricity costs. This is true in the long term, despite a higher initial cost.
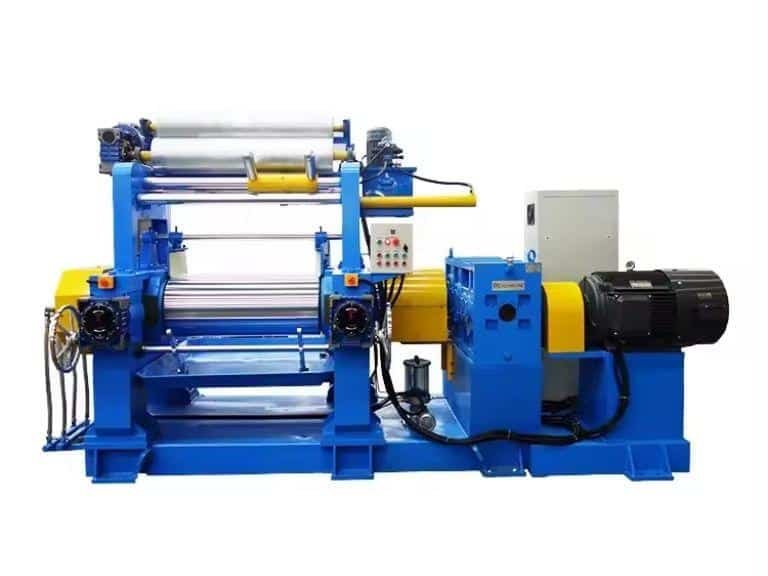
The benefits of the right choice of calender
Picking the right rubber calender is key to business growth. It can greatly improve product quality and productivity. It also slashes operating costs.
The right calendar can ensure product consistency and accuracy. It makes high-quality rubber and reduces defects through precise nip adjustment and stable operation.
Picking an efficient calender can boost production. It cuts cycle time, raises output, and meets market demand. It makes the enterprise more competitive.
Choosing a machine with low maintenance needs and high energy efficiency can cut long-term operating costs a lot. Reducing downtime, cutting energy use, and reducing parts replacement frequency helps. It lets companies get a better return on investment and lower operating costs.
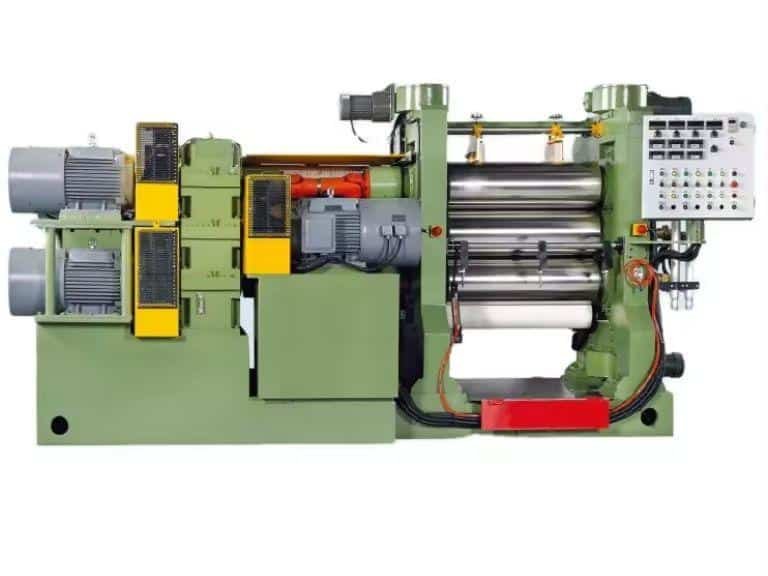
Maintenance and upkeep
Regular lubrication: Ensure that all moving parts remain well-lubricated to minimize wear and tear.
Regular Cleaning: Clean the drum and other key parts often. This prevents rubber and impurities from building up. It keeps the machine in good condition.
Inspection and replacement of damaged parts: Regularly inspect the rollers, motors, and transmission. Replace damaged parts promptly.
Calibration and adjustment: Make sure the equipment’s parameters are normal. Regularly calibrate and adjust it to ensure precision and quality.
Regular training for operators: The training is for operators. It ensures they know the operating rules and maintenance requirements of the machine. This knowledge helps them avoid failures and risks from improper operation.
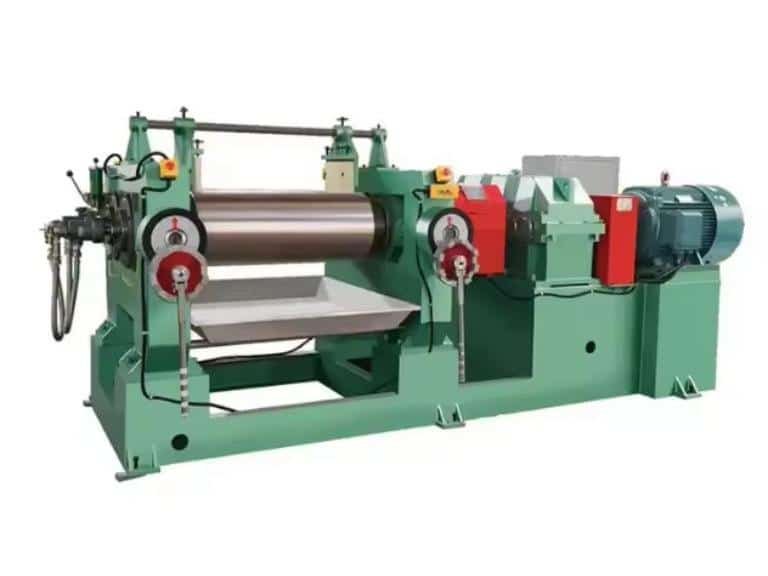
Conclusion
The right machines and equipment directly affect productivity and quality. They are vital for the success of a company. Enterprises can assess business needs, machine specs, costs, and other factors to select the right calender equipment. Regular maintenance and repair are also necessary, as they extend the calender’s service life and ensure it runs efficiently, improving the enterprise’s competitiveness. If you need help with rubber calenders, you can contact Crowns Machinery engineers for professional help!
FAQ
A rubber calender usually lasts 15 to 20 years. It depends on factors like the machine’s quality, the production environment, the specific use, and how often it’s used and maintained.
Decide how often to maintain a rubber calendar based on its use and the production environment. Usually, it is recommended to do a routine inspection once a month. Do a full maintenance once every six months. This will ensure the stable operation of the machine and extend its life.