Crowns Machinery’s Rubber Vulcanizing Press Equipment plays a vital role in the rubber manufacturing process. Raw rubber is processed into various shapes, like tires and seals. This happens through vulcanization at high temperatures and pressures. So, using and maintaining rubber vulcanizing press equipment is key. It’s vital for efficiency and quality. This article will focus on how to correctly operate and maintain these equipment to ensure their long-term stable operation and maximize their performance.
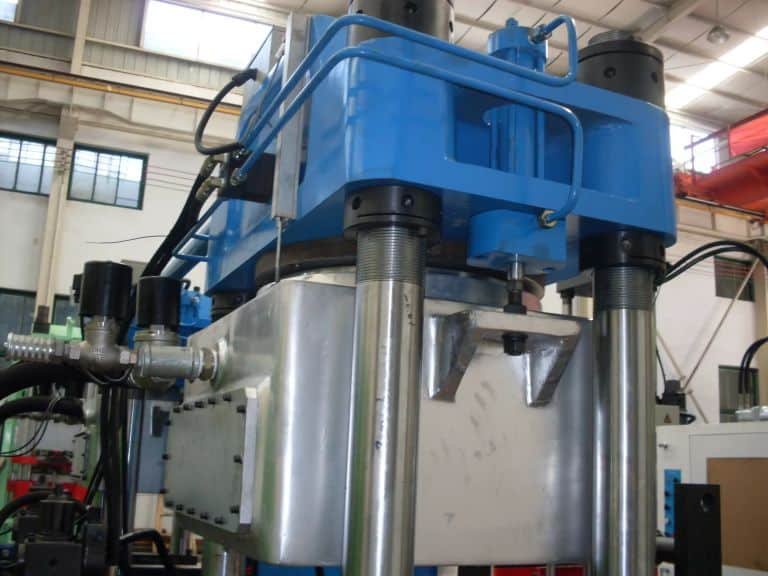
Table of Contents
Understanding the Role of Rubber Vulcanizing Press Equipment
Vulcanization is a key process. It turns raw rubber into a finished product. The product has better elasticity and durability. Through high-temperature and high-pressure vulcanization, the molecular structure of rubber chemically reacts to form a stronger, more elastic product. This process is critical to the quality of the final product. It affects things from automotive tires to medical appliances. The accuracy of vulcanization directly affects product performance and longevity.
Crowns Machinery‘s rubber vulcanizing presses play a key role in this process. Our equipment is designed to provide stable, uniform high temperature and high pressure. It ensures that each batch of product meets strict quality standards. Below are some of the key features of Crowns Machinery’s vulcanizing presses:
Quality Manufacturing: Crowns Machinery uses advanced manufacturing processes. We use quality materials to make sure our equipment is durable and reliable. Our equipment can run reliably for a long time. It can do so under tough production conditions. This minimizes downtime due to equipment failure. It also ensures efficient and continuous production.
Performance Advantage: Our equipment is designed to be energy efficient, reducing production costs by optimizing energy consumption. At the same time, precise systems control temperature and pressure. They ensure consistency and accuracy in the vulcanization process. This leads to optimal quality from batch to batch. The modular design makes maintenance easy. It also allows for upgrades based on needs.
Wide Range of Applications: Crowns Machinery’s vulcanizing presses are used in making many types of rubber products. These include automotive tires, industrial seals, medical devices, and consumer goods. Our equipment meets the tough requirements for rubber product performance in different industries. It helps our customers to stand out from fierce competition. It also helps them to improve the competitiveness of their products.
Guidelines for Proper Usage of Rubber Vulcanizing Press Equipment
Proper operation of rubber vulcanizing press equipment is critical to ensure safe and efficient production. When using Crowns Machinery equipment, operators should follow these steps and precautions.
Equipment Inspection And Preparation: Before starting operation, the operator should inspect the equipment. They should do this to ensure there are no loose or damaged parts. Check the pressure and temperature control systems to make sure they are in proper working order. In addition, make sure the work area around the equipment is clean and free of obstructions to ensure safe operation.
Loading and Preheating: Load the rubber products into the equipment correctly. Do this to ensure even distribution and avoid partial loading. Turn on the machine’s preheating function. Set the temperature and pressure according to the product requirements. Make sure the machine reaches the intended working condition. This process is crucial to ensure the vulcanization effect.
Vulcanization Process Control: The operator should monitor the equipment during vulcanization. They should check its temperature, pressure, and time. Avoid making adjustments while the equipment is running to prevent accidents. If adjustment of parameters is required, it is important to follow the operating procedures step by step to ensure safety.
Unloading and cooling: After vulcanization, unload the products safely. Do this according to the operating procedures to avoid burns from high temperatures. Let the equipment cool. This will ensure it gets back to a safe temperature before the next use. This not only ensures the safety of the operator but also maintains the normal operation of the equipment.
Cleaning And Maintenance: After each operation, the operator should clean the equipment. They should do this to remove leftover rubber and impurities. Regularly inspect critical equipment parts. Maintain them to keep them in good condition. Lubricate the moving parts, check the electrical system, and replace worn parts in time to extend the service life of the equipment.
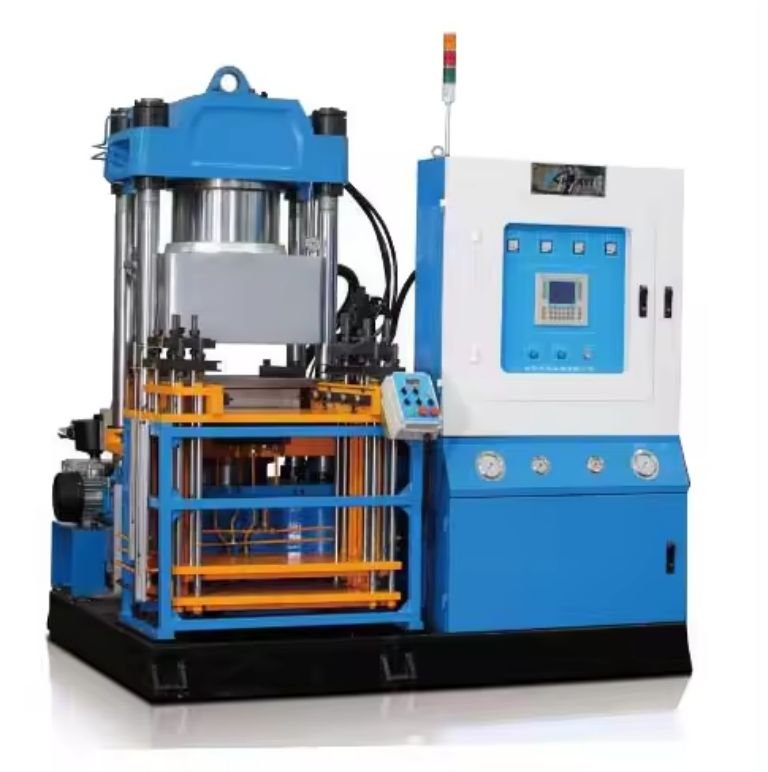
Maintenance Procedures
Crowns Machinery equipment is designed for easy operation. It has intuitive controls and detailed operator guides. These features ensure that operators can easily learn to use the equipment. Also, we provide thorough operator training. It ensures that every operator is skilled and safe in using the equipment. This boosts productivity and product quality. Our customer support team is ready to answer your questions. They will provide technical help to ensure your production runs smoothly.
You must do routine maintenance. It is essential to keep your rubber vulcanizing press equipment stable for a long time. This is a routine maintenance program for Crowns Machinery equipment. It includes specific steps for cleaning, lubrication, and inspections.
Cleaning: After each operation, the operator should thoroughly clean the equipment. Use the right cleaners and tools. They remove leftover rubber and dirt. This is especially important after vulcanization. Keeping equipment surfaces and operating areas clean has two benefits. It helps extend equipment life and prevents contaminating the next batch.
Lubrication: Regular lubrication of the equipment’s moving parts is essential to keep it running smoothly. Use the proper lubricant to oil bearings, gears, and rails. Do this according to the equipment manual. Use a moderate amount of lubricant. This avoids overuse, which can cause too much friction or part contamination.
Periodic Inspection: Conduct a thorough equipment inspection once a month to ensure that all parts are in good working condition. Check the accuracy of temperature and pressure control systems. Check that they are working properly within their set ranges. Look at the electrical system to make sure there are no loose or damaged wires and connectors. Pay special attention to worn parts, such as seals, screens, and drive belts, and replace worn parts promptly.
Common Issues and Troubleshooting Techniques
When using rubber vulcanizing pressure equipment, operators may encounter a variety of problems. Below are some common problems and recommended solutions from Crowns Machinery:
Poor product quality can result from uneven temperatures or erratic control. The key to solving this problem is to check the temperature sensors and heating elements to make sure they are working properly and are clean and undamaged. Calibrate the temperature control system regularly and replace faulty parts if necessary. Also, keep the heating area clean. This will avoid residue that could affect heating and ensure even temperatures.
Insufficient or Fluctuating Pressure: Insufficient or fluctuating pressure can affect vulcanization results. To fix this problem, operators should check the hydraulic system. They should ensure that there is enough fluid and no leaks. Change the hydraulic fluid often. Clean the hydraulic pump and screens. This will ensure the hydraulic system works well. Check the pressure sensors and regulators. Fix or replace them as needed. This will keep the pressure stable.
Equipment failure or shutdown: Sudden shutdown or equipment failure can seriously affect the production schedule. The operator should first check the electrical system to ensure that all connectors and wires are not loose or damaged. Regularly inspect and maintain critical components. These include motors, pumps, and control panels. Doing so prevents sudden breakdowns. Keeping the equipment clean helps. It also helps to prevent dust and contaminants from entering the electrical system. This will reduce the incidence of breakdowns.
Difficulty releasing product from the mold: Difficulty releasing product from the mold can reduce productivity. Solving this problem requires checking the mold surface. If it’s not smooth, polish it. Use an appropriate release agent and make sure it is evenly applied to the mold surface. Regularly check the condition of the mold and replace or repair damaged molds to ensure smooth release.
Excessive Noise or Vibration: Unusual noise or vibration during operation may indicate an equipment problem. Solutions include checking equipment fastening to ensure all bolts and connections are tight. Lubricate moving parts often to cut friction. Check motors and pumps. Repair or replace them as needed. Keep equipment running smoothly to minimize noise and vibration.
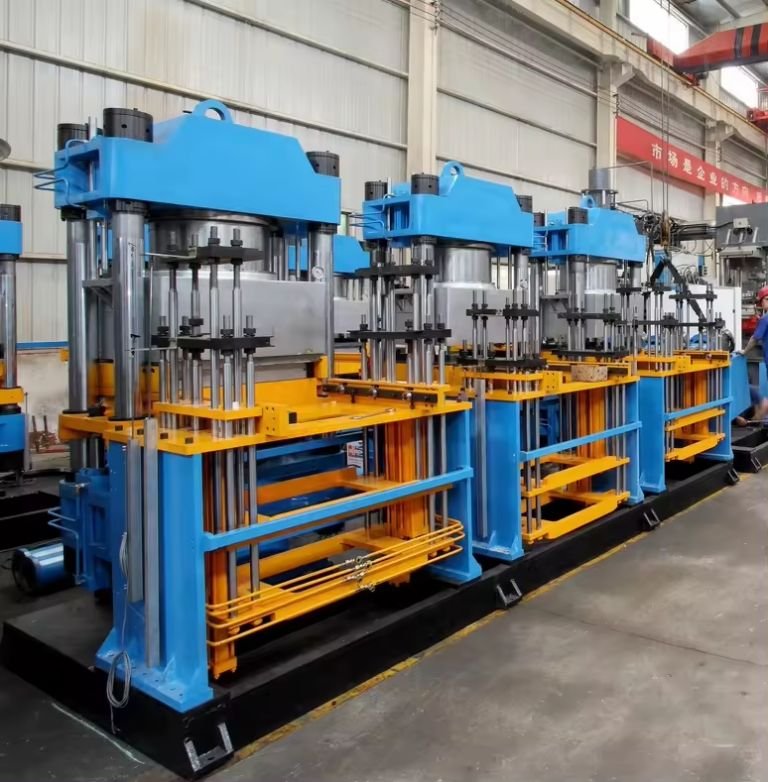
Conclusion
To get the best performance from their equipment and ensure production continuity, rubber manufacturers are encouraged to follow proper operation and maintenance guidelines. Regular cleaning, lubrication, and inspection can catch problems early. They can prevent downtime from equipment failure. Preventive maintenance not only improves productivity and product quality, it also extends the life of your equipment.
Crowns Machinery commits to providing top-quality equipment and service. We achieve this through technological innovation and service optimization, ensuring every customer benefits from our equipment. Our customer support team is always ready to help. They provide technical support to ensure your production is smooth and worry-free. If you use and keep up your equipment right, you’ll unlock the full potential of your Crowns Machinery gear. It will let you produce efficiently and reliably. Contact our team today for solutions!
FAQ
Our rubber vulcanizing pressure equipment is for various types of rubber products. These include automotive tires, rubber hoses, seals, and rubber flooring.
The capacity of our equipment varies depending on the model and configuration. We offer a wide range of equipment. It has various specifications and production capacities. It meets the needs of different customers.
The use of our equipment requires strict adherence to safety procedures. Operators must wear appropriate personal protective equipment (PPE) and receive relevant training. The equipment is also equipped with safety protection devices to ensure the safety of the operator and the equipment.
We recommend regular equipment maintenance to ensure proper operation. The frequency of maintenance depends on the equipment model and usage. In general, we recommend basic cleaning and lubrication each month. We also recommend more thorough inspections and maintenance regularly.
We offer a comprehensive range of support and services to our customers. This includes equipment installation and commissioning, operator training, regular maintenance, and troubleshooting. Our customer service team is always available to help and support you.
Yes, our equipment comes with a warranty. The exact warranty period and terms will be confirmed with the customer at the time of purchase. We also offer extended warranties and maintenance programs. They ensure the equipment will operate well for a long time.
Yes, we offer customization services. We design and make equipment to fit our customers’ specific needs. Please contact our sales team and we will provide you with a customized solution.