Rubber Vulcanizing Press are vital in manufacturing. They ensure durable, high-quality rubber products are made. The machines are essential for many industries. These include automotive, aerospace, and consumer goods. They need a precise and efficient vulcanization process.
Understanding the cost of a Rubber Vulcanising Press is vital for potential buyers and businesses. Knowing the factors that affect price can help you make informed buying decisions. It ensures the right balance between quality and budget.
As we delve into the factors that affect the cost of a rubber vulcanizer, we’ll explore the various aspects that buyers need to consider. This guide will help you understand the cost-cutting factors available when buying a Rubber Vulcanising Press from Crowns Machinery.
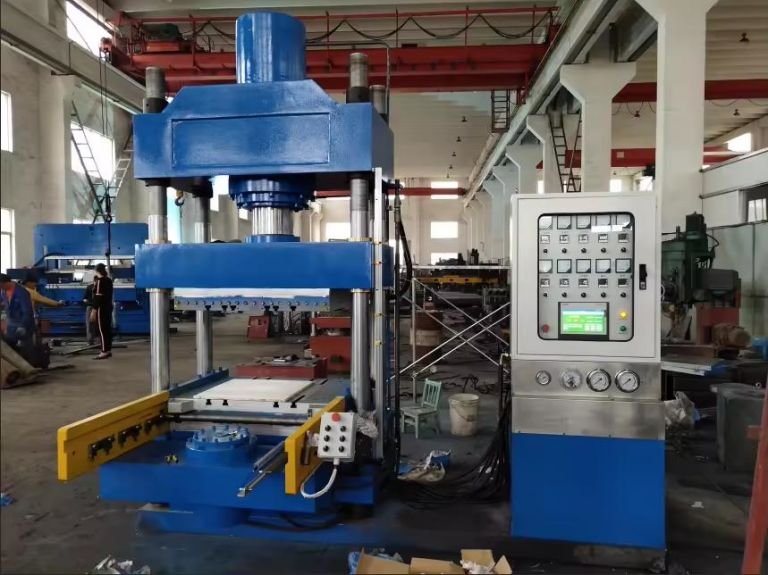
Table of Contents
What is a Rubber Vulcanizing Press?
A Rubber Vulcanizing Press is a special machine. It is used to turn raw rubber into a finished product. It does this through the process of vulcanization. The process involves applying heat and pressure to the rubber, causing a chemical reaction that strengthens and stabilizes the material. A vulcanizing machine’s main purpose is to improve rubber products. It makes them more elastic, resilient, and better overall.
The basic operation of a vulcanizing machine involves placing the rubber material into a mold. The vulcanizing machine then applies high pressure and controlled heat to the mold to initiate the vulcanization process. The key components of a vulcanizing machine include the hydraulic system, the heating plate, the mold, and the control panel. The hydraulic system creates the needed pressure. The heating plates ensure the temperature control is consistent and precise. The control panel allows the operator to set and watch the vulcanization process’s parameters. This ensures the best results.
Vulcanising Presses are vital. They are used in many industries, including automotive, aerospace, and consumer goods. In the automotive industry, these vulcanizers are used to manufacture tires, seals, and hoses, which require high durability and performance. In the aerospace industry, vulcanized rubber components are vital. They can withstand tough conditions and stresses. They keep aircraft safe and reliable. Consumer products, like footwear and sports equipment, also rely on vulcanized rubber. It improves their performance.
The benefits of using vulcanizing machines in production are manifold. Vulcanized rubber products offer excellent strength, elasticity, and abrasion resistance. The process also improves the material’s chemical, heat, and weather resistance, making it suitable for a variety of demanding applications. Also, vulcanizing machines provide precision and consistency. They let manufacturers make high-quality rubber parts efficiently and reliably.
Factors Influencing the Cost of a Rubber Vulcanizing Press
Size and Capacity
The size and capacity of a rubber vulcanizing press significantly impact its cost. Larger presses can handle more rubber. They are more expensive because they need more materials and engineering. For example, a small press makes rubber seals. It might cost less than $10,000. But, a large press for heavy-duty tire production could cost over $100,000.
Different sizes cater to various applications. Small to medium-sized presses are often used in the production of consumer goods, automotive parts, and smaller industrial components. But, large presses are essential for heavy industry. They are used in applications such as tire and large-scale rubber part production.
Type of Press
The type of press also plays a vital role in determining the cost. Manual presses require more operator intervention and are usually less expensive than automatic presses. Automatic presses use advanced control systems and automation to speed up vulcanization. This raises productivity but also costs more.
There is a difference between a platen press and an injection molding machine. A platen press uses flat, heated plates to press and vulcanize rubber, while an injection molding machine injects rubber into a mold before applying heat and pressure. Each type has its own advantages and costs. These depend on the specific needs of the production process.
Customization Options
Customization options can greatly affect the price of a rubber vulcanizing press. Custom-built presses designed to meet specific production requirements often cost more than standard models. Common customizations include specialized heating elements, custom mold designs, and additional safety features. For instance, a press with custom-sized molds makes unique rubber components. Or, it has advanced temperature control. It will cost more than a standard press.
Materials and Build Quality
The types of materials used in constructing a rubber vulcanizing press also influence its cost. High-quality materials, like stainless steel and hardened alloys, ensure durability and longevity. But, they cost more. Sturdy materials make presses that can withstand tough use. They need less maintenance and replacement. This can justify their higher initial cost.
Build quality is another critical factor. A well-constructed press with high-precision engineering offers better performance and reliability. Cheap, poorly built presses cost less at first. But, they can lead to more maintenance and downtime. These issues hurt production efficiency and cost-effectiveness in the long run.
Technology and Automation
Advanced technological features and automation significantly affect the cost of a rubber vulcanizing press. The press has features. These include programmable logic controllers (PLCs), touch-screen interfaces, and automated loading and unloading systems. They improve the press’s functionality and efficiency, but they also raise the price.
Automation reduces the need for manual work. It cuts labor costs and improves consistency in production. Automated systems can precisely control temperature, pressure, and timing, ensuring optimal vulcanization results. The initial automation investment is higher. But, the long-term benefits are higher productivity and lower costs. They are usually worth the initial spending.
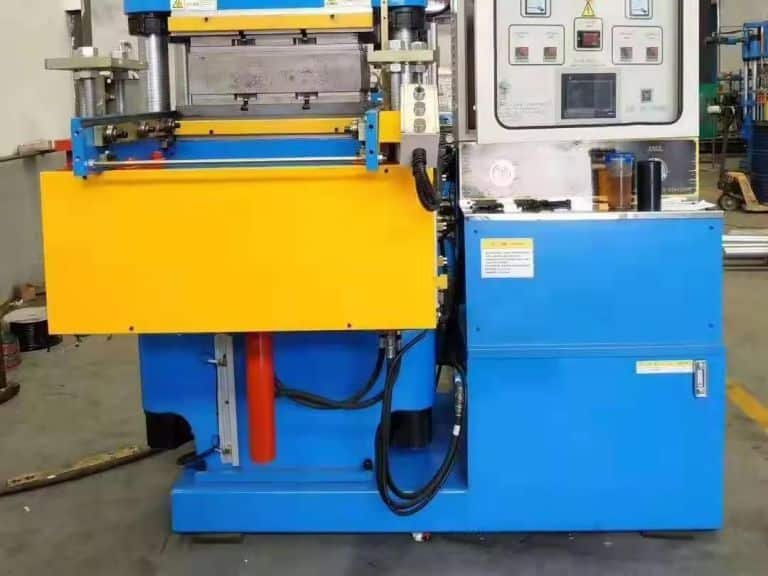
Additional Costs to Consider
Installation and Training
Costs to install a rubber press include transport, setup labor, and facility modifications. These can range from a few thousand to tens of thousands of dollars. Proper training is crucial for efficient and safe operation, reducing the risk of accidents and improving productivity. Companies like Crowns Machinery often provide on-site training, online courses, and detailed manuals. These are important investments for long-term efficiency.
Maintenance and Repairs
Maintenance costs cover routine inspections, lubrication, part replacements, and system calibrations. Regular maintenance helps avoid big repairs. It also cuts downtime, ensuring steady performance and extending the machine’s life. Over time, these precautions can save a lot. They also improve reliability.
Energy Consumption
Operating a vulcanizing press is energy-intensive, with costs varying based on press size, usage, and local energy rates. Larger presses typically consume more electricity. To reduce energy costs, businesses can:
Use energy-efficient presses with features like programmable logic controllers (PLCs).
Maintain equipment to ensure peak efficiency.
Implement energy management systems to monitor and control consumption .
How to Choose the Right Vulcanizing Press?
Choosing the right vulcanizing press involves several key considerations. First, assess your business needs. Do this by figuring out production volume, product specs, and needed automation. Match these requirements with press specifications to ensure optimal performance and cost-efficiency.
When evaluating suppliers, look for those with strong reputations. They should also have quality certifications (like ISO or CE) and good after-sales support. Reading customer reviews and testimonials can give valuable insights. They show the supplier’s reliability and service quality.
Crowns Machinery offers customized solutions. We are tailored to specific production needs, ensuring high-quality and efficient operations. Our support includes installation, training, and maintenance. It makes them a trusted choice for businesses that need reliable vulcanizing presses.
Carefully assess your needs. Choose a reputable supplier. This will ensure that your investment in a vulcanizing press meets your production goals.
Conclusion
Understanding the cost and factors influencing the price of rubber vulcanizing presses is crucial for making informed decisions. Key factors include the size, type, customization, materials, and technology of the press. Crowns Machinery offer high-quality, cost-effective solutions. The solutions are tailored to meet diverse industrial needs. For more information or to request a quote, contact Crowns Machinery today.
FAQ
The average lead time for a rubber vulcanizing press is 8 to 12 weeks, including production, quality checks, and shipping. Customizations may extend this timeframe.
Yes, Crowns Machinery offers custom-built vulcanizing presses. They come with features like special molds, advanced controls, and better safety systems. These features are tailored to your needs.
Crowns Machinery provides a one-year warranty. It covers parts and labor. They also offer extended support services to ensure efficient operation.
Maintain your press with monthly inspections, lubrication, and timely part replacements. Annual comprehensive maintenance is recommended to ensure optimal performance.