Co-extrusion is key in modern manufacturing. It makes complex, high-performance rubber products. This technology combines many rubber materials into one product. It offers unique benefits. These benefits are in terms of strength, flexibility, and functionality. Co-extrusion can combine different materials. This creates parts that meet the needs of many applications, such as seals, gaskets, and hoses. This process improves rubber products. It enhances their physical properties and makes them last and perform better under various conditions.
In the following sections, Crowns Machinery will explain rubber co-extrusion. It will explore the process, discuss the equipment, and present the advantages and uses in various industries.
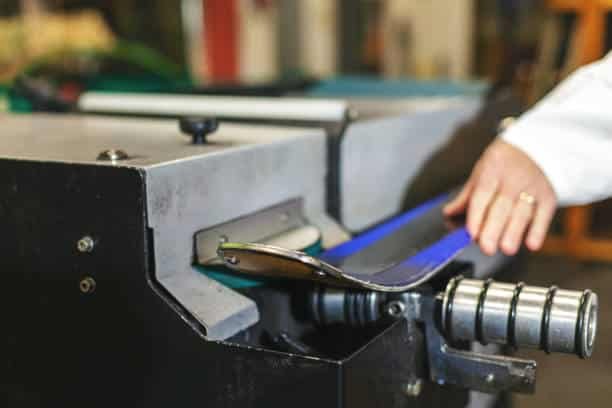
Table of Contents
What is Rubber Co-Extrusion?
Rubber co-extrusion is the process of extruding two or more rubber materials at once. This is done through a single die to make a unified product. This technique allows manufacturers to combine different materials. Each material adds specific properties to the final product. By using co-extrusion, manufacturers can make complex profiles. The profiles have varying hardness, flexibility, and color. They are tailored to meet specific application needs. The product is co-extruded. It benefits from the unique qualities of each material used. This setup enhances its overall performance, durability, and functionality in diverse conditions.
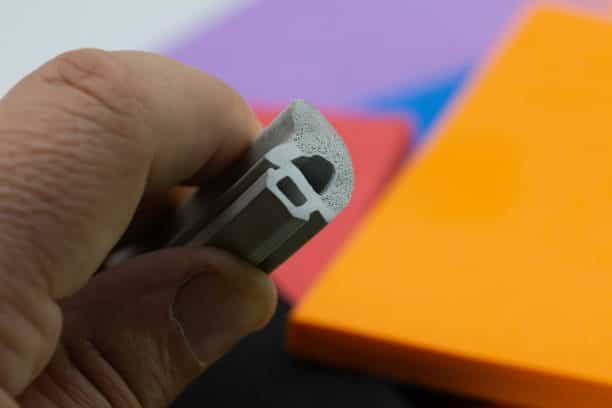
The History and Evolution of Rubber Co-Extrusion
The history of rubber co-extrusion dates to the mid-20th century. Then, manufacturers began to explore ways to improve rubber product performance. Over the years, technological advancements have made the process more efficient and versatile. Early co-extrusion techniques were limited by available technology. But, modern machinery and materials have made the process more advanced and reliable. Today, rubber co-extrusion is vital in industries like automotive, construction, and electronics. It allows for making high-performance parts with precise, steady quality.
The Rubber Co-Extrusion Process
Step-by-Step Guide to Rubber Co-Extrusion
Material Selection: Choosing the right rubber compounds is crucial. The chosen materials must work together. They must have the properties we want. These include flexibility, durability, and resistance to the environment.
Preparation: We mix the chosen rubber materials and preheat them. This ensures they are uniform. It also ensures they have optimal conditions for extrusion.
Extrusion: The prepared materials are fed into the co-extrusion machine. The machine extrudes the materials through a single die. This forms a cohesive product with multiple layers or sections.
Cooling and Curing: After extrusion, the product is cooled to maintain its shape. Then it cures. This involves heating to set the rubber’s properties and ensure durability.
Final Inspection: Checks to ensure the product meets standards. They are conducted by quality control. This includes inspecting for defects and verifying the material properties.
Equipment Used in Rubber Co-Extrusion
Extruders: The machines push the rubber materials through the die. This shapes them into the desired profile. Co-extrusion typically involves multiple extruders working in tandem to handle different materials .
Dies: Tools that shape the extruded material into specific profiles. The die’s design is critical. It shapes the final product.
Cooling Systems: They cool down the extruded product quickly. This keeps it keeping its shape and strength. Good cooling is vital. It prevents bending and keeps the product’s quality.
Curing Ovens: Used to cure the rubber by heating it to specific temperatures. This process makes the material stronger and stretchier. It also sets the final shape of the product.
Advantages of Rubber Co-Extrusion
Strength and Durability: Rubber co-extrusion allows for combining different materials. Each adds to the strength and durability of the final product. This method ensures that the end product can handle stress and wear. It is suitable for demanding uses.
Flexibility and Elasticity: By picking materials with specific properties, manufacturers can get the flexibility and elasticity they want. This is critical for products. They need to keep their shape and work well in changing conditions.
Thermal and Chemical Resistance: Rubber co-extrusion improves the product’s heat and chemical resistance. This is vital for applications in harsh environments. Combining materials gives the product longevity and reliability. The materials have superior resistance to heat and chemicals.
Material Efficiency: Rubber co-extrusion is highly efficient in terms of material usage. By controlling material flow and combining compounds, manufacturers can cut waste a lot. This efficiency lowers material costs. It also helps make production more sustainable.
Production Efficiency: The co-extrusion process streamlines production by enabling the simultaneous extrusion of multiple materials. This reduces the time required to produce complex rubber products and minimizes labor costs. Faster production and less manual work save manufacturers a lot of money.
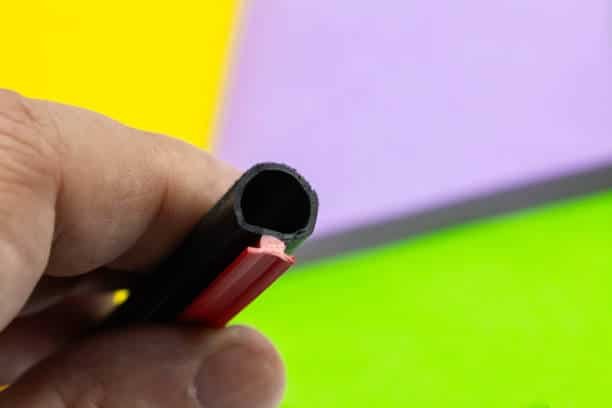
Applications of Rubber Co-Extrusion
Rubber co-extrusion has many uses across various industries. Each benefits from the unique properties and versatility of co-extruded rubber.
Automotive Industry: Rubber co-extrusion is vital in the automotive sector. It is used to make critical parts that ensure vehicle performance and safety. High-performance seals and gaskets are used in engines and doors. They prevent leaks and keep conditions optimal. Also, they make durable and flexible hoses and tubes. They are co-extruded to endure the rigors of moving fluids in the vehicle, like coolant, fuel, and hydraulic fluids.
Construction Industry: Rubber co-extrusion is vital in construction. It seals and insulates buildings. Weatherstripping is made through co-extrusion. It provides effective seals for windows and doors. This enhances energy efficiency and weather resistance. Rubber profiles are used for thermal and sound insulation. They are co-extruded to create barriers. The barriers minimize heat loss and dampen sound transmission. This improves the comfort and sustainability of buildings.
Electronics Industry: The electronics industry relies on rubber co-extrusion. It is used to make parts that ensure the reliability and function of electronic devices. Rubber has protective layers. They are co-extruded to insulate electrical cables. They protect the cables from the environment and stress. Also, we use co-extruded rubber to make keypads and buttons. They provide durability and responsiveness in electronic devices. This ensures smooth operation and user satisfaction.
Challenges and Solutions in Rubber Co-Extrusion
Rubber co-extrusion is hard during production. But, clever solutions overcome these obstacles. They ensure high-quality and consistent results.
Rubber co-extrusion often faces the challenge of ensuring different rubber materials are compatible. It is critical to ensure that these materials bond well together to create a bonded product with uniform characteristics. Another challenge is to keep quality consistent between batches. This requires careful attention to detail and effective quality control.
To meet these challenges, manufacturers use advanced machines. For example, they use Crowns Machinery’s top Rubber Extruder Machine to control extrusion precisely. These machines can extrude many materials at once. This ensures the product sticks well and is uniform. Also, we use strict testing protocols to verify the co-extruded product’s quality. They help us find and fix problems early in production.
Conclusion
Rubber co-extrusion is a key process in modern manufacturing. It creates complex, high-performance rubber products by extruding multiple rubber materials at once. This tech improves product strength, flexibility, and functionality. It also brings many benefits and solutions to many industries. Many industries have benefited from rubber co-extrusion technology. It is used in automotive, construction, and electronics. It makes high-quality, efficient products that meet the needs of specific applications. Rubber co-extrusion faces many challenges. But, we can solve them with top equipment and strict quality control.
If you are looking for a customized rubber extrusion solution, please feel free to contact Crowns Machinery. We have the tech and experience. We can give you pro advice and custom services to meet your needs.
FAQ
Materials such as EPDM, silicone, and nitrile are commonly used in rubber co-extrusion. These materials have specific properties. They include flexibility, durability, and chemical resistance. This makes them suitable for many uses.
Rubber co-extrusion improves product quality. It allows the mixing of materials with different properties. Co-extrusion integrates many rubber materials into one product. This improves performance, durability, and functionality. It meets specific application requirements well.
The automotive, construction, and electronics industries are major beneficiaries of rubber co-extrusion. These industries rely on co-extruded rubber products. They use them for critical components like seals, gaskets, weatherstripping, insulation, cable insulation, and keypads, among others.
The initial setup costs for rubber co-extrusion can be high. This is due to the need for special equipment and materials. But, the long-term cost savings are big. Co-extrusion is cost-effective. It saves on material and labor costs. This is due to using materials and making products faster.
Co-extrusion involves extruding multiple materials at once through a single die. It allows for making complex products with layers or sections. In contrast, traditional extrusion typically involves the extrusion of a single material. Co-extrusion offers more versatility. It offers flexibility in design and composition. It lets us make customized parts with better performance.