Rubber vulcanizing machines are important equipment for manufacturing rubber products. They convert raw rubber into a final product with specific qualities. These qualities include elasticity, strength and durability. The vulcanization process ensures that rubber products meet these needs. This step is critical to improving product quality and performance.
Crowns Machinery is a leading manufacturer of rubber vulcanizers. We provide reliable and efficient vulcanization solutions to customers worldwide. The company has many years of experience and utilizes advanced technology.
Crowns Machinery continues to innovate to meet the changing needs of the market. We work to improve the productivity of rubber products and help customers succeed in a competitive market.
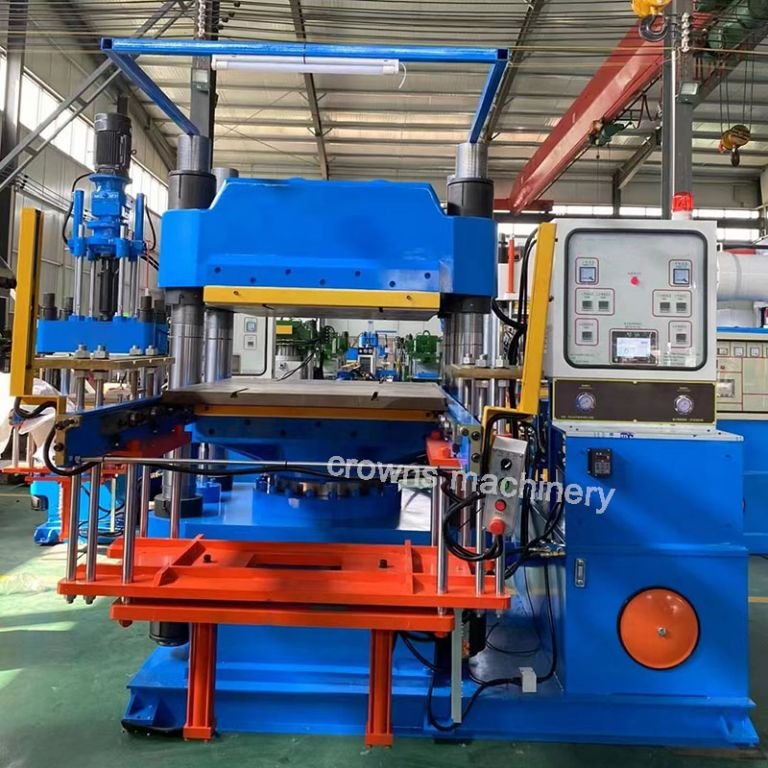
Table of Contents
Preparation before operation
Preparation before operation is essential to ensure smooth operation and improve work efficiency. First, checking the condition of the equipment is an essential step.
Ensure that the unit’s power supply, cables and control panel are working properly. Check for visible damage or faults.
Maintain and clean the unit regularly. This helps prevent problems that could affect operation.
Next, check that the working environment meets safety standards. Ensure that the operating area is clean, tidy, free of obstructions and well ventilated. Check that there is proper lighting so that the operation process can be clearly viewed. Also, make sure that the environment is free from factors that could interfere or cause danger.
Finally, make sure that the required tools and materials are available. Prepare all the tools required for the operation, such as molds, in advance and check that they are in good condition.
Additionally,Make sure the amount and specifications of materials, like rubber compounds, are correct. This helps avoid missing or mismatched materials during the process.
With these preparation steps, problems in operation can be minimized and work efficiency and safety can be improved.
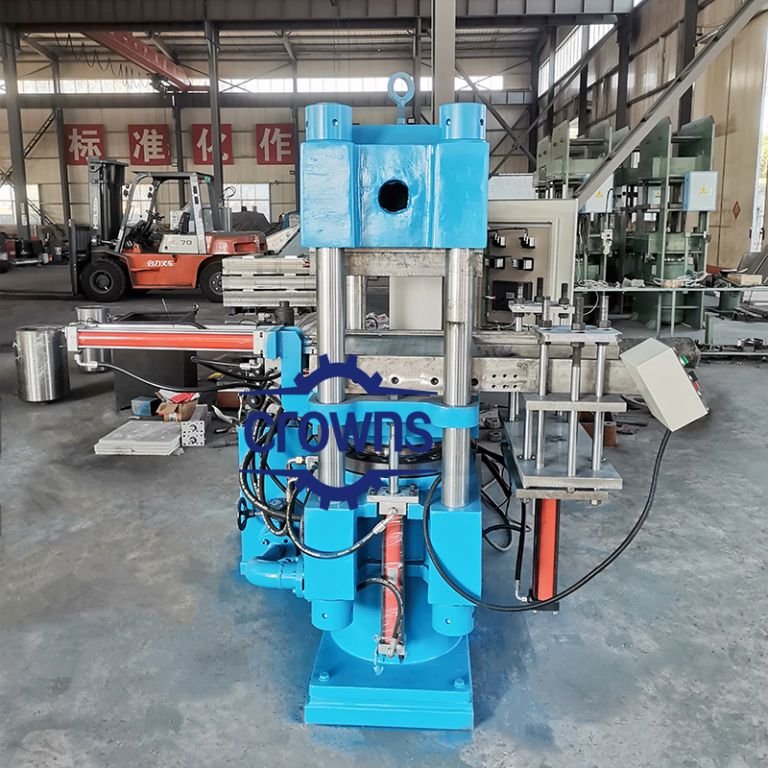
Mold Installation
Selecting and installing the right mold is an important part of running a rubber vulcanizer. The first step is to select a mold that matches the production requirements and the design of the rubber product. Consider the type and size of the mold based on these requirements.
When installing molds, make sure they are properly aligned in the machine. Tighten the fixing bolts securely to prevent the mold from moving or deforming during vulcanization.
Make sure the mold surface is clean and undamaged. This is important to obtain a good surface quality for the final rubber product.
After installation, perform a no-load test. This helps to confirm that the mold is working properly in the machine.
Preparation of rubber compound
The preparation of the rubber compound directly affects the quality of the final product. Firstly, suitable rubber materials and additives should be selected. Then, mix them according to the product requirements.
Ensure that each ingredient is accurately weighed in the specified proportions. Mix thoroughly in a mixing machine until the mixture is smooth and homogeneous. A homogeneous and consistent mixture is essential for the vulcanization process. Avoid air bubbles or unevenness during the mixing process.
After mixing, store the mixture in a clean, airtight container. This prevents contamination and deterioration and keeps the mixture in optimal condition for use.
Heating and Curing Process
First, set the correct vulcanization temperature and time. This is usually based on the rubber formulation and product requirements.
The control system automatically heats the mold when the vulcanizer is started. It maintains the temperature and pressure at set levels.
Throughout the process, the temperature and pressure are monitored to ensure they remain within the required range. This ensures uniform vulcanization. Sensors help track real-time changes to prevent overheating or underheating.
When vulcanization is complete, the system automatically stops heating. The rubber is then cooled for a set period of time to allow it to fully cure and reach a safe temperature for further processing.
Removing the finished product and mold cleaning
When removing the finished product, do so carefully to avoid damage to the product or equipment. Use the right tools to gently take out the vulcanized rubber, avoiding the use of too much force.
After removing the product, clean the mold to remove any remaining rubber or impurities. Use a mild detergent and a soft cloth. Avoid harsh cleaners that can damage the mold.
After cleaning, inspect the mold to make sure it is not damaged. Regular maintenance will help extend the life of the mold. Regular inspection and maintenance will keep the mold performing well and extend its life.
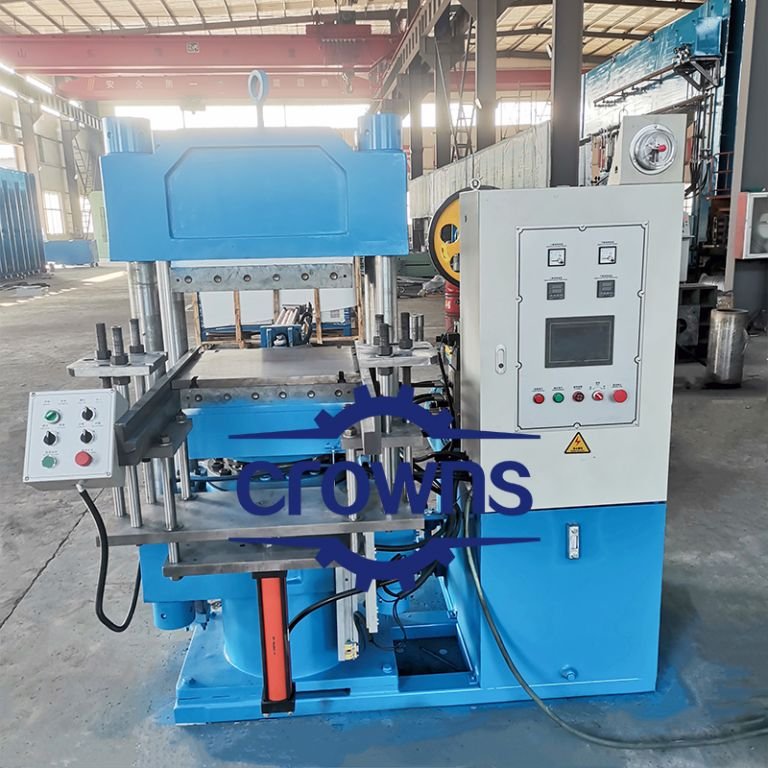
Safety Precautions
Reasonable safety precautions are essential when operating a rubber vulcanizer.
First, ensure that the operator wears the necessary personal protective equipment, such as heat-resistant gloves and goggles.
Second, familiarize yourself with the equipment’s operator’s manual for emergency shutdowns and troubleshooting.
Precautions for handling high-temperature and high-pressure equipment:
Be careful of high temperatures and pressures when operating the vulcanizer. Avoid direct contact with heating parts and pressure relief devices to prevent burns or other accidents.
Regularly check the machine’s safety devices, such as overheat protection and pressure safety valves. Make sure they are working properly to prevent any potential safety hazards.
Conclusion
Knowing how to use a rubber vulcanizing machine is important for smooth production and good product quality. Rigorous preparation for operation, precise mold setup, accurate rubber mixing, regulated heating for vulcanization, and mold cleaning can effectively increase productivity and ensure consistent product.
Crowns Machinery has been manufacturing rubber equipment for many years. We specialize in providing high quality machines and expert support. Our goal is to help rubber manufacturers improve their production processes and product quality.
If you’re interested in a vulcanizing machine, contact Crowns. We can provide more details and a price quote. Crowns will help you improve production efficiency.
FAQ
Common problems during vulcanization?
Bubbles: If the rubber mixture is not homogeneous or if the material is of poor quality, bubbles can occur.
Solution: Make sure the mixing equipment is working well and the rubber is mixed correctly.
Incomplete vulcanization: This can occur if the temperature or vulcanization time is not correct.
Solution: Check and adjust the machine’s temperature, pressure and time settings to ensure they are accurate.
How do I extend the life of my molds and equipment?
Regular Maintenance: Clean molds and check for wear regularly. Lubricate and tighten parts as needed to prevent damage.
Correct Operation: Always follow proper operating procedures. Avoid overloading or improper use of the machine to ensure long life and smooth operation.