Crowns Machinery’s rubber mixing mill is a key piece of equipment in manufacturing rubber compounds. These rubber compounds are used in the production of rubber products such as tires, seals and hoses. How it works is really quite simple. It mixes natural or synthetic rubber with a number of additives, such as fillers and vulcanizing agents, to make the rubber material we need. The benefit of this type of machine is that it makes the quality of rubber more consistent. It also improves the elasticity, strength and durability of the material. Whether for mass production or customized needs, a rubber mixer is an indispensable tool.
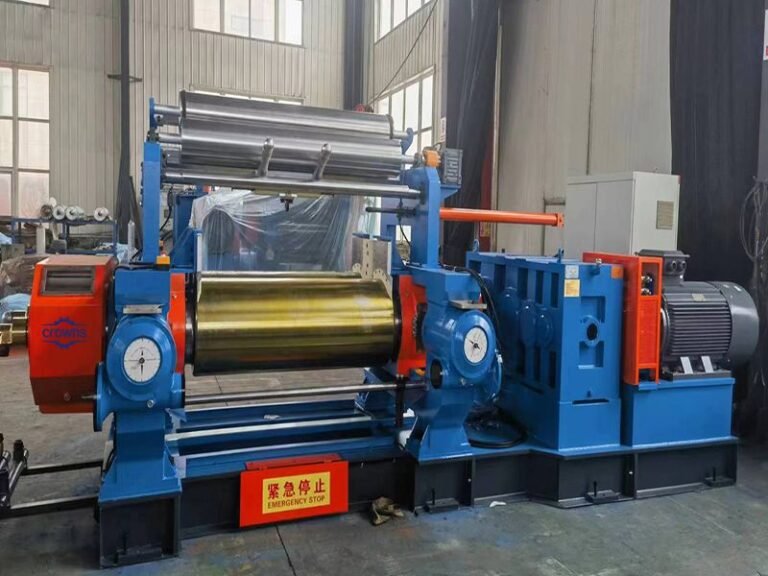
Table of Contents
What is a rubber mixer?
Rubber mixer is a machine that mixes rubber with different additives. It’s often used to make rubber products like tires and hoses. Its main job is to evenly combine natural or synthetic rubber with fillers, reinforcements, and softeners. This makes sure the rubber performs well during production. The machine works by stretching, pressing, and folding the rubber with two rotating rollers. It keeps mixing the material until everything is fully blended. The rollers’ temperature can be adjusted to make sure the rubber doesn’t get too hot or cold, which helps maintain its quality. The main parts of the rubber mixer are:
Roller: Mainly used to mix the rubber and additives evenly.
Transmission system: Provides power for the mixing process and ensures smooth running of the machine.
Rubber mixing machine main use
Rubber mixers play an important role in many industrial sectors, especially in tire manufacturing. Its main role is to evenly mix different types of rubber (e.g. natural and synthetic rubber) with various chemical additives to ensure stable material properties. Through mechanical action, the mixer is able to evenly distribute the chemical components of the rubber, such as fillers, vulcanizing agents, reinforcing agents, etc., so that the rubber has better physical characteristics and processing properties.
Tire Manufacturing
The rubber mixer is vital in the tire manufacturing process. It ensures that the rubber material used to produce the tread, sidewall, etc. of a tire has uniform quality and consistent properties. The compounded rubber not only meets the requirements in terms of hardness and elasticity, but also adapts to a variety of harsh driving environments, thus extending the life of the tire.
Industrial Sectors
In addition to tire manufacturing, rubber compounders are widely used in the production of seals. Through a precise mixing process, the seals are produced with excellent pressure and wear resistance. These seals can be used in a wide range of machinery and industrial equipment. In addition, it plays an important role in the manufacture of hoses and conveyor belts. By carefully mixing the materials, the rubber mixer ensures that these products are strong and flexible enough to work well.
Other areas
Rubber compounders also play a role in a number of other areas, including:
Rubber shoe sole production: to provide abrasion-resistant rubber materials for footwear manufacture.
Automotive parts: for the production of rubber fittings with good elasticity and durability.
Construction sealants: to ensure the weather resistance and stability of sealing materials.
Conclude
At Crowns Machinery, we design, manufacture, and sell high quality rubber mixing equipment. Our equipment is used in a wide range of industries such as tires, seals, hoses, and conveyor belts. This equipment helps ensure that your rubber is always well mixed and of the highest quality. Whether you’re working with natural or synthetic rubber, our mixers make the production process faster and more accurate. Whatever your needs, Crowns Machinery is committed to providing you with a customized solution.
FAQ
Usually adjusted to the type of material, the temperature range is 50-200°C.
It can handle a wide range of elastomers such as natural rubber, synthetic rubber, and silicone.
Selection is based on production volume, material viscosity and roller size.