A rubber extruder is a key piece of equipment used to process rubber products. It can be adjusted flexibly according to different production requirements. For example, by changing the die head and adjusting the extrusion volume. This allows the production of different specifications of rubber products. Indispensable equipment for the production of rubber products and other daily necessities. It improves production efficiency and product quality. It also reduces production costs and operating difficulties.
Troubleshooting critical performance in:
Ensure product quality: Faults in the production process will cause a variety of parameters in the extrusion process to go out of control. Ultimately, this will affect product quality.
Guarantee the normal operation of the equipment: The rubber extruder has problems. We need to fix them soon to avoid delaying production.
Guarantee the safety of equipment and personnel: Equipment failure will lead to dangerous operations. This can cause personal injury to staff and other serious consequences.
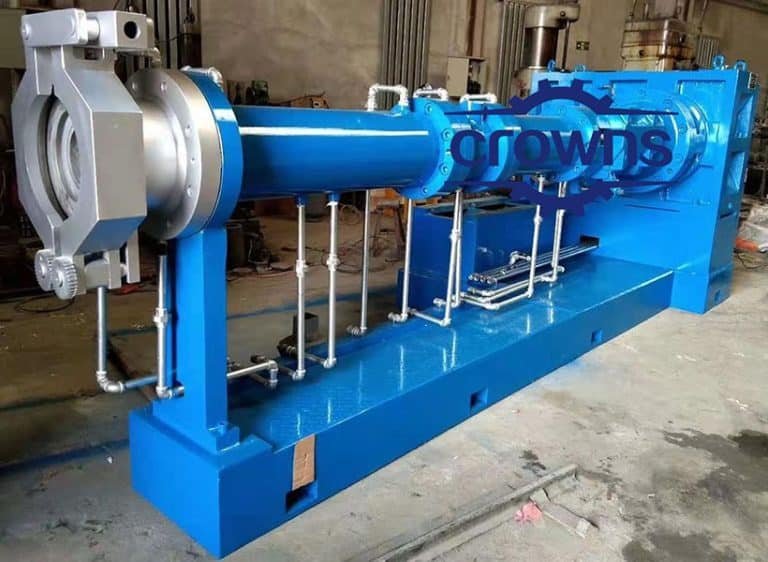
Table of Contents
Common rubber extruder failure
Rubber extruders commonly fail due to barrel clogging, temperature control issues, and screw wear. The emergence of these problems will negatively impact production efficiency and quality. Let’s analyze these issues specifically.
Barrel clogging problem: Improper rubber mixing ratio or impurity accumulation can often clog the rubber extruder barrel. This prevents proper extrusion of the raw material. It interrupts production and affects product quality.
Temperature control problems: When the extruder’s temperature control system fails, it can’t accurately control the extrusion temperature. This results in uneven heating of the extrusion process. It affects the final product quality.
Screw wear problem: The extruder screw will change over time due to long-term use. This will cause unstable extrusion pressure. This reduces output. It also impacts product surface smoothness and final product quality.
Troubleshooting process
Problem diagnosis: Understand the details of the failure. Observe the equipment in operation. Pay attention to abnormalities, such as noise. Check the temperature control, pressure control, and other systems linked to the extruder.
Cause analysis
Confirm whether the operation of the equipment is by the specifications.
Check whether the quality of raw materials used is qualified
Check whether the screw, die head, and other parts of the equipment are damaged.
Check whether the electrical system is faulty.
Judge the nature and severity of the fault: Determine the fault’s severity based on its impact on product quality and productivity.
Solution formulation and implementation
Take urgent measures to deal with serious faults on a priority basis.
Develop a detailed maintenance plan, including the replacement of necessary parts.
Ensure through training that operators are aware of the correct operation of the equipment.
Adjust the system parameters according to the production demand to ensure the normal operation of the equipment.
Verify that equipment faults are effectively solved through verification.
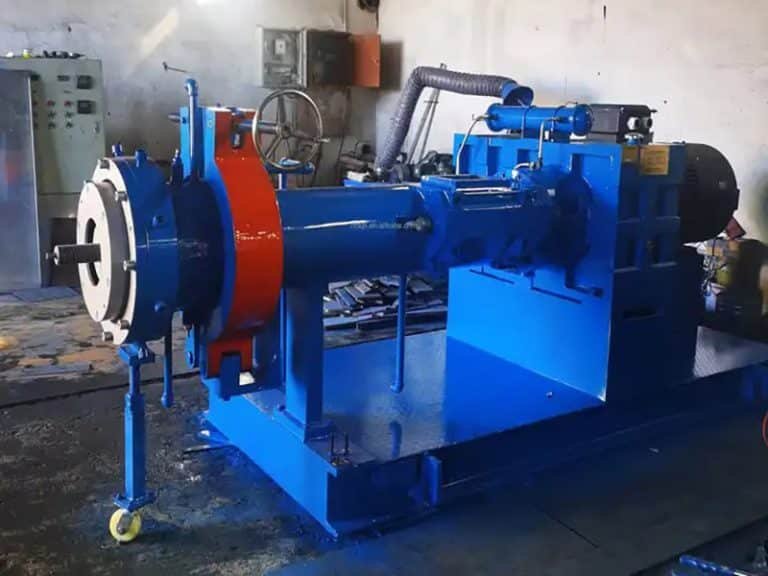
Barrel cleaning and maintenance
Regularly clean and maintain the rubber extruder’s barrel to prevent clogging and ensure product quality.
Barrel cleaning procedures and related recommendations are as follows:
Disconnect the power supply. Make sure the equipment is cooled down after a complete shutdown.
Clean all residues from the inside of the barrel.
Regularly check the inner wall of the barrel for any abnormal corrosion or wear. Repair or replace it in time.
Clean the screw and agitator to ensure that no foreign matter is attached. Check the screw for wear and tear, and replace it in time.
Check the barrel heating system. Clean the dust and impurities in the system in time to ensure stable heating.
Check the lubrication of screw, bearing and other parts, add or replace the lubricant in time.
Make a good record of daily maintenance and cleaning for subsequent tracking.
Handling of temperature control problems
The temperature control problem of a rubber extruder usually has many reasons. These include sensor failure, heating element damage, control system failure, and personnel operation.
Sensor failure: Temperature sensors may be faulty or out of order. They need to be checked and calibrated regularly.
Heating element damage: Prolonged use may damage the temperature control system’s heating element. Inspect and replace it regularly.
Control system failure: Once the control system fails, it will not accurately control the production temperature. The system should be checked regularly for circuit connection and system calibration. Damaged parts should be repaired and replaced in time.
Operator error operation: The operator doesn’t know enough about the operating procedures. This has led to improper temperature settings. The relevant personnel should be trained, and the equipment should be controlled by authority. This will prevent arbitrary changes and interference.
Screw and die head maintenance
The rubber extruder screw and die head need regular maintenance and repair. This will extend its service life and improve production efficiency.
Regular cleaning of the screw and die head: should be cleaned of impurities and residues at the end of each use to prevent clogging.
Check and replace the worn parts: Regularly check the screw and die head for abnormal wear and tear. Make timely repairs or replacements to avoid affecting product quality.
Check the related fasteners to prevent the bolts and nuts from loosening.
Check the runner and outlet of the die head. Make sure they are not blocked or deformed. This will keep the extrusion work smooth and unobstructed.
Check the heating system of the die head. This includes the heating element, temperature sensor, and more. Ensure it’s operating normally.
Safety issues and emergency measures
The rubber extruder operates at high temperature and pressure. Other factors also pose danger. As a result, safety is crucial.
Operators must undergo relevant operation training before starting work. This is to ensure they are familiar with the equipment’s safety and standard operating procedures.
Operators should wear high-temperature gloves and other relevant personal protective equipment. This will help them avoid direct contact with high temperatures and prevent burns.
Strictly follow the correct operating procedures for the equipment operations.
Stay away from screws, molds, and other moving parts. This ensures that protective measures are in place.
Conduct regular equipment inspections. Ensure that all systems and components are working properly.
Emergency measures are recommended as follows:
Train operators in emergency first aid measures. This will ensure they can be rescued in time if accidents occur.
Develop an emergency plan and related handling procedures. Ensure that emergencies can be handled in an orderly manner.
Press the emergency stop button when an abnormal situation occurs. The button is configured in the equipment. It stops the machine in time.
Once the equipment fails, it should be repaired in time to eliminate potential safety hazards.
Extruder performance monitoring and data analysis
The implementation of extruder performance monitoring and data analysis mainly relies on the application of sensors and data analysis systems. This improves production efficiency and reduces production costs.
Sensors: Sensors include temperature, pressure, and extrusion force sensors. Using these sensors during production, you can monitor temperature and pressure changes in real time and detect rubber extrusion abnormalities. This helps you investigate and solve issues promptly.
Data analysis: Timely data collection through the monitoring system and big data analysis help discover potential anomalies. This allows for early detection and prevention of possible failures, timely maintenance, and reduced equipment downtime. As a result, production efficiency improves and production costs decrease.
Conclusion
In summary, manufacturers can achieve early prevention and greatly reduce the risk of failure by focusing on extruder maintenance and troubleshooting. It is critical to follow the correct steps and methods for troubleshooting to improve production efficiency, reduce production costs, and ensure product quality.