Rubber extrusion is a common method in the rubber industry. Rubber is pushed through a die to form a specific shape. Rubber extrusion technology plays a key role in providing customized solutions. It is particularly important in areas like medical devices and sports equipment.
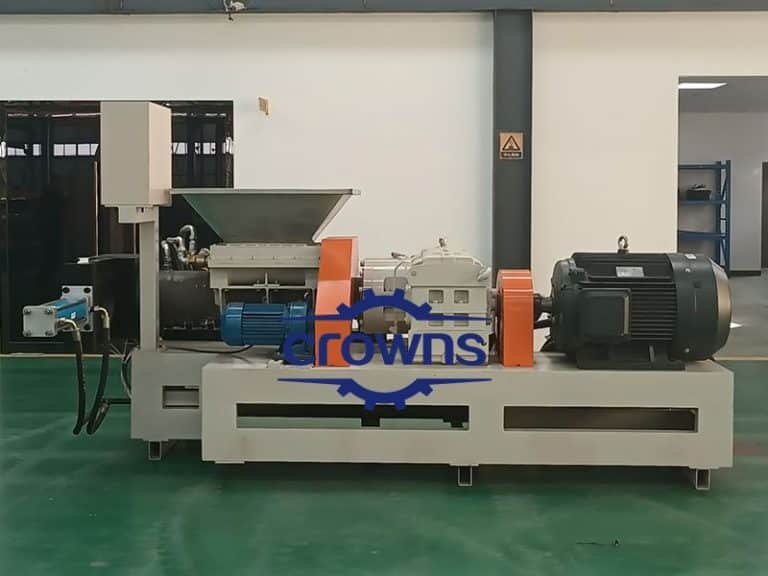
Table of Contents
Key takeaway
Customizing rubber products is crucial because various industries need different sizes, shapes, and properties. Extrusion technology produces customized products meeting customer needs, giving the rubber industry a competitive edge. This flexibility serves various industries and applications.
Precision requirements are another key factor in rubber extrusion technology. Precise dimensions and shapes are crucial for the device’s performance and safety in medical device manufacturing. Precise control of rubber thickness and density in shoe sole manufacturing impacts comfort and durability. Precise extrusion processes in sports equipment manufacturing can improve athletes’ performance by ensuring excellent stability and performance.
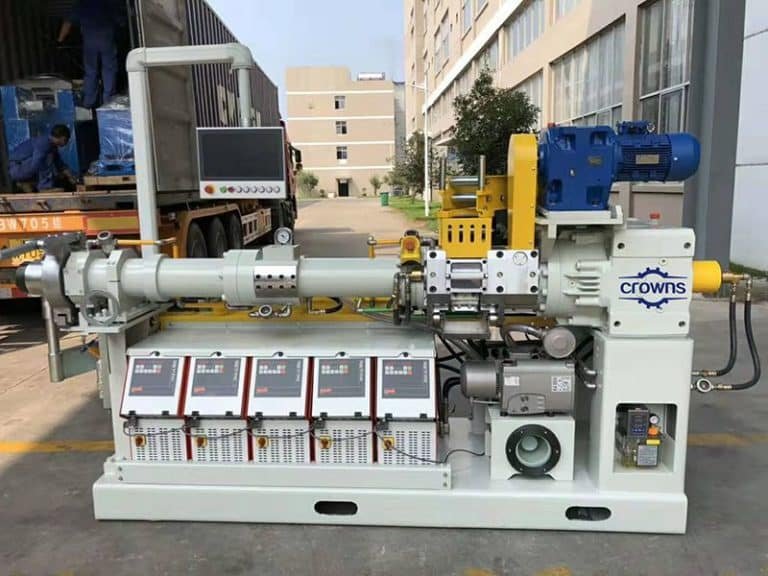
Demand for customization
With the pursuit of performance, comfort, and personalization of products in various industries, there is an increasing demand for the customization of rubber components. This is because customized rubber components can meet the specific needs of different industries and users, as analyzed below:
Shoe sole industry
Comfort requirements: Customised rubber soles can be designed according to the needs and walking habits of different users, providing a better fit and more comfortable soles.
Personalization and fashion requirements: With consumers’ pursuit of personalization of shoes, more and more attention is paid to the fashion and aesthetics of shoes, and customization is particularly important. Customized rubber soles can be flexibly designed according to the trend and personalization requirements, thus satisfying consumers’ pursuit of personalization aesthetics and fashion.
Medical Device Industry
Accuracy and safety: Rubber parts for medical devices often require high levels of accuracy and reliability to ensure the safety of the device. Customized rubber components can be designed to meet specific medical device design requirements, ensuring precision in size and shape to meet the medical industry’s needs for safe treatment and accurate diagnosis.
Sports equipment industry
Performance optimization: Sports equipment has high performance and durability requirements, and customized rubber components can be specifically designed to optimize performance for different sports.
Shock absorption and protection: Many sports equipment require rubber components to provide excellent shock absorption and protection. Customized rubber components can be designed according to the athlete’s body weight and movement style, providing more professional shock absorption and reducing the chance of injury during sports.
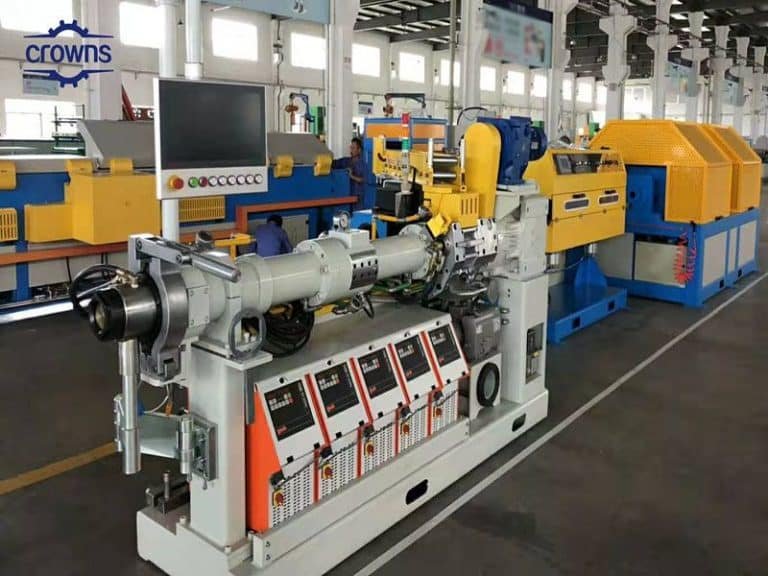
Advances in precision extrusion technology
In recent years rubber extrusion technology has made remarkable progress in terms of precision and efficiency, mainly thanks to the following two innovations:
Advanced control system: modern rubber extruders are equipped with advanced control systems, these systems can real-time monitoring and adjustment of the extrusion process, such as temperature, pressure, speed, and other parameters, to improve the stability of the production process, to ensure the precision and consistency of product quality.
Advanced mold design and manufacturing technology: mold is an important part of the rubber extruder, and is one of the key factors affecting extrusion accuracy. With the development of CAD CNC and other computer technologies, the precision of mold design has been greatly optimized, improving the precision and performance of the products.
Case Study
Case: An automotive manufacturer needed customized rubber sealing strip fittings for the sealing and noise protection functions of car doors and windows. And these seals needed different sizes and shapes to suit different car models.
Solution: The manufacturer introduced rubber extrusion technology, designed customized molds for the seals according to the needs of different car models through CAD, and used excellent rubber materials to successfully produce customized products that meet the standards of the automotive industry, ensuring the dimensional accuracy and reliable performance of the seals.
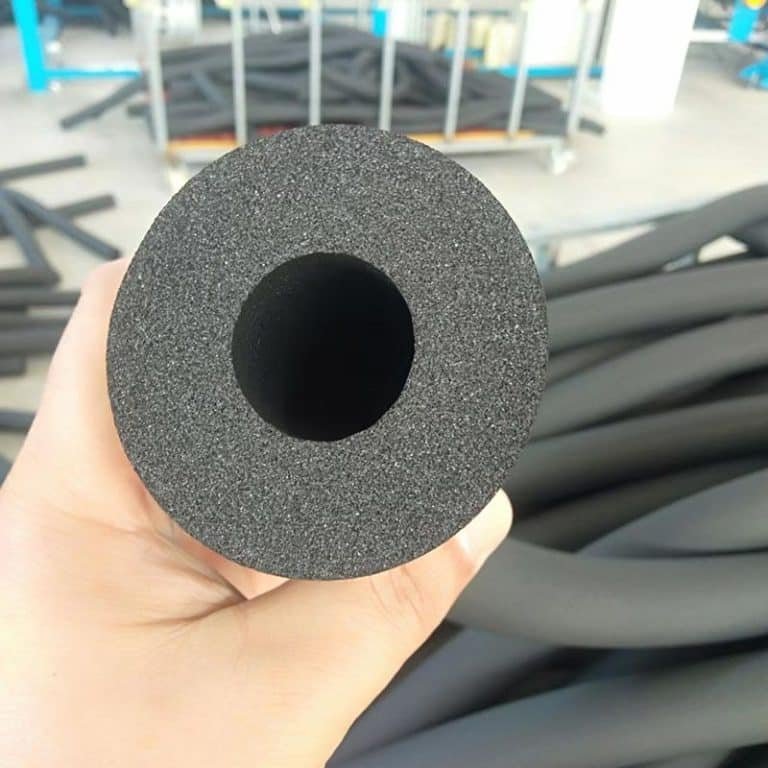
Challenges and Solutions
The challenges that may be faced during customized production using rubber extruders are summarised below:
Inability to realize complex sizes and shapes: If a customer requires a rubber product that is very complex and has specific size and shape requirements, a conventional extruder may not be able to meet these requirements.
Solution: Use CAD/CAM and other technologies for mold design to ensure that the complex shapes required by the customer can be manufactured accurately. At the same time, choose the right rubber material and adjust the parameter settings of the extrusion process to ensure that the precision and consistency of the shape are maintained during the extrusion process.
Material compatibility issues: Some industries may have specific requirements for material performance and compatibility, such as the medical device industry, where biocompatibility requirements are quite stringent.
Solution: Work with rubber manufacturers to select medical-grade rubber that meets the requirements, ensure that the extruder’s extrusion system and die are compatible with the chosen material, and take proactive cleaning and disinfection measures to ensure that medical products are produced in compliance with medical industry standards and regulations.
Production efficiency and production cost control: Customised production processes often require more investment in manpower and time, which is likely to result in lower production efficiency and higher production costs.
Solution: Increase production efficiency by using automated and intelligent extruder equipment that reduces human intervention. Use advanced production planning systems to optimize production processes and reduce production costs.
Quality control and consistency: Customised production processes need to ensure product quality and consistency, but can be affected by the variability of the extrusion process.
Solution: Develop rigorous quality control procedures and adopt advanced monitoring equipment to monitor and adjust relevant parameters in real-time during the extrusion process to ensure that the product meets the specifications. And comprehensive inspection of the extruded products is carried out to ensure that the quality of the final products meets the customer’s requirements.
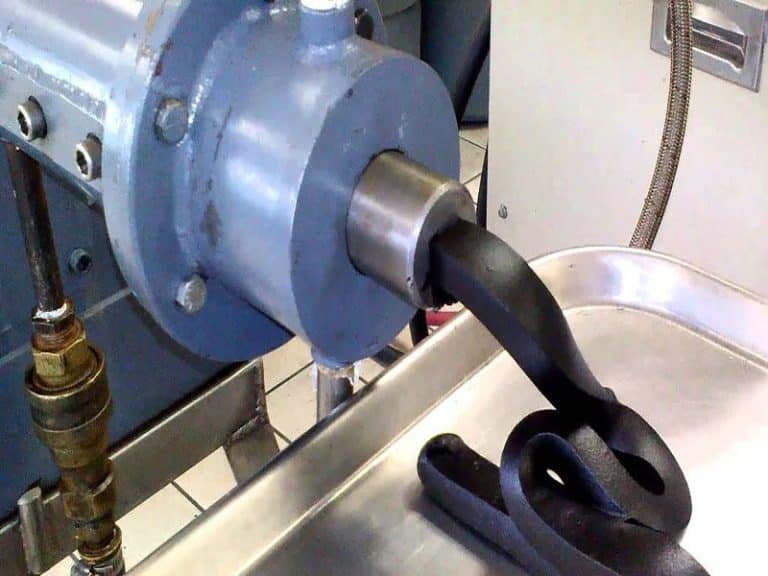
Summary
With the increasing demand for customized rubber products in industries such as medical devices, automotive parts, and construction materials, the continuous progress of rubber extrusion technology provides important technical support for the customization needs of various industries. Enterprises can perfectly meet all the customization needs of their customers and realize the production, as long as they make full use of the advantages of extrusion technology while adopting appropriate solutions to meet the challenges they face. Optimizing the production process and gaining a competitive edge in the marketplace.