Rubber vulcanizing molds play a key role in the rubber manufacturing process. The molds determine the shape, size, and performance of the final product. So, choosing the right mold is crucial. It ensures product quality and production efficiency. Good molds speed up production. They also cut scrap and costs.
When selecting a mold, think about the material, design complexity, durability, and cost. Each application may need different mold materials. These include liquid silicone rubber (LSR), high consistency rubber (HCR), and room temperature vulcanized (RTV) rubber. Each material has unique benefits and uses. Choosing the right one can greatly boost productivity and product quality.
Crowns Machinery is a top maker and seller of rubber vulcanizers. We have lots of experience and expertise. Our product offering covers a wide range of vulcanizers and mold solutions to meet the needs of different industrial sectors. In this article, we will look at how to choose the best rubber vulcanizing mold. It will help you get the best results in your production.
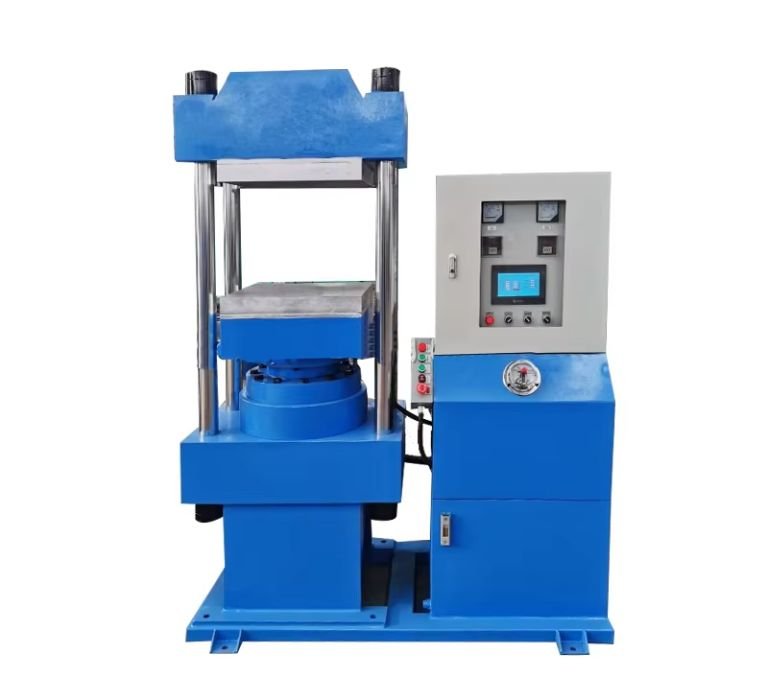
Table of Contents
Basic Types of Curing Molds
When choosing a vulcanizing mold, knowing the basic types and their uses can help. It can help manufacturers pick the best one for their production needs and products. Crowns Machinery offers many high-quality vulcanizing molds. The molds meet the needs of different industries and applications.
Fixed molds and movable molds
Fixed molds: Fixed molds are designed for the production of large quantities of standardized products. These molds are simple and strong. They can withstand high pressures and temperatures for long periods. This makes them good for continuous mass production. Fixed molds have two advantages. They are consistent and efficient. These traits make them great for making products that need homogeneity, like tires and seals.
Movable molds: Movable molds are suitable for the production of diverse and complex products. These molds have adjustable parts. They allow the production of different shapes and sizes in one mold. This provides greater flexibility. Moving molds are great for small production runs. These runs need frequent changes in product specs. This includes custom rubber parts and lab samples.
Single-Cavity vs. Multi-Cavity Molds
Single Cavity Moulds: These molds produce only one product per vulcanization. They work for small batches or large products. This type of mold is simple in design and inexpensive to manufacture but is relatively inefficient. Single cavity molds are great for products that need high precision and quality control. These include large industrial rubber parts and complex custom products.
Multi-cavity molds: Multi-cavity molds can make many products at once during each vulcanization. They are good for making many small products quickly. Multi-cavity molds are tough to design. But they boost output and slash costs per product. They are often used for mass production. This includes consumer goods, medical supplies, and small industrial parts.
Key factors in selecting a mold
Product design and complexity
Select the right type of mold based on the design complexity of the product. For products that require high precision and detail, it is even more important to choose a mold with fine processing capabilities. High-precision molds can capture subtle design elements and ensure that every detail of the product is perfect. For example, for products that need detailed designs, liquid silicone rubber (LSR) molds are best. This is because of their low viscosity and ability to replicate intricate details.
Material Selection
Picking a durable mold material is critical. It must be suitable for the production environment. This is key to ensuring mold life and productivity. Below are a few commonly used mold materials and their application scenarios:
Liquid Silicone Rubber (LSR): LSR molds are suitable for detailed designs. They provide high precision and smooth finishes. They are for demanding applications, like medical devices and electronic components.
High Consistency Rubber (HCR): better suited for robust and durable applications. HCR molds make stronger, longer-lasting parts for mass-produced industrial goods and consumer products.
Commonly used vulcanization mold materials
When selecting a mold material, it helps to understand the properties and applications of each material. This understanding helps you make the best decision. Crowns Machinery offers many high-quality vulcanizing mold materials. They can meet the needs of many industries and applications.
Natural Rubber
Natural rubber is a commonly used vulcanizing mold material for standard applications. It is relatively inexpensive, but in some cases, a release agent may be required to prevent the product from sticking to the mold. Natural rubber molds are suitable for a variety of general-purpose rubber products such as tires, seals, and gaskets.
Silicone Rubber
Silicone rubber is a mold material with excellent properties for products that require a high-quality surface finish. Silicone rubber molds offer a better surface finish and easier release. This makes them widely used for products that need fine detail and smooth surfaces, like medical devices and electronic parts.
RTV (Room Temperature Vulcanized) Rubber
RTV rubber, or room-temperature vulcanized rubber, is good for low-temperature uses. It is ideal for handling fragile or complex materials. RTV rubber molds cure without heat. So, they are good for small-scale or lab production. The material is flexible and easy to work with, making it ideal for complex or delicate molds.
Mold Design and Manufacturing
Mold Design
Mold design is a key component to ensure productivity and product quality. During the design process, the hardness, flexibility, and detail requirements of the mold need to be considered. The mold’s hardness and flexibility determine its ability to withstand high pressure and heat. It must also keep stability and durability during production. Detail requirements determine the fineness and surface finish of the final product.
When designing a mold, special attention needs to be paid to the following points:
Hardness: The mold material should be hard. Its hardness should match the needed pressure and temperature in production. Hard mold materials are harder. They can resist wear and bending better. They are good for high-pressure, high-temperature production.
Flexibility: Flexible mold materials have an advantage in detailing. This is especially true when making complex and delicate products. Liquid Silicone Rubber (LSR) is one such material that is highly flexible and suitable for high-precision molds.
Detail requirements: The mold design for such products must capture and reproduce fine details. High-precision mold design ensures consistent, high-quality products.
Mold Manufacturing
Choosing a professional mold maker is an important step in ensuring the accuracy and quality of your mold. Professional manufacturers have high-tech equipment. They also give full support and service. This keeps the molds in good shape during production.
In the process of mold manufacturing, the following aspects are particularly important:
Precision: The precision of the mold directly affects the quality of the product. High-precision molds can ensure the accuracy and consistency of product dimensions.
Quality: The manufacturing quality of the mold determines its service life and productivity. Choosing top mold materials and advanced processes can greatly boost mold durability and productivity.
Maintenance and Care
Inspect and clean your molds regularly to ensure they are in optimal working condition. Regular maintenance can prolong the service life of the mold and reduce downtime during production. Inspect the mold after each use. Remove residues and waste promptly to keep them from affecting the next use. For metal molds, anti-rust treatment is also required, especially when stored for a long period. Regularly lubricate the moving parts of the molds and choose the right lubricant to reduce friction and prolong service life. When storing molds, the environment should be kept dry and clean to avoid humidity and extreme temperatures. Molds should be placed in special racks or cabinets to avoid deformation or damage caused by stacking or irregular placement. With these steps, you can keep the molds in top condition. This will make them last longer and boost production and product quality.
Conclusion
Choosing the right rubber vulcanizing mold requires considering many factors. These include product design, material choice, and mold build quality. Crowns Machinery offers a full range of vulcanizing solutions to help customers improve their production process and product quality. Contact Crowns Machinery for more information or to receive a quote.
FAQ
Depending on the material and frequency of use, the life of a mold can be several years.
Yes, Crowns Machinery offers customization services to meet specific production needs.
Cleaning after each use and regular thorough inspections and maintenance are recommended.