Crowns Machinery knows the critical role rubber vulcanizing presses play. They are vital to many industries. These presses are crucial for making rubber products better. They are used in industries from cars to planes. Our expertise in manufacturing and selling high-quality vulcanizing presses ensures that we meet the diverse needs of our clients.
The purpose of this article is to help businesses choose the right rubber vulcanizing press. By understanding the main factors, you can make informed choices. They will improve your productivity and product quality. Let us guide you through the key aspects. Consider them when selecting a vulcanizing press that meets your needs.
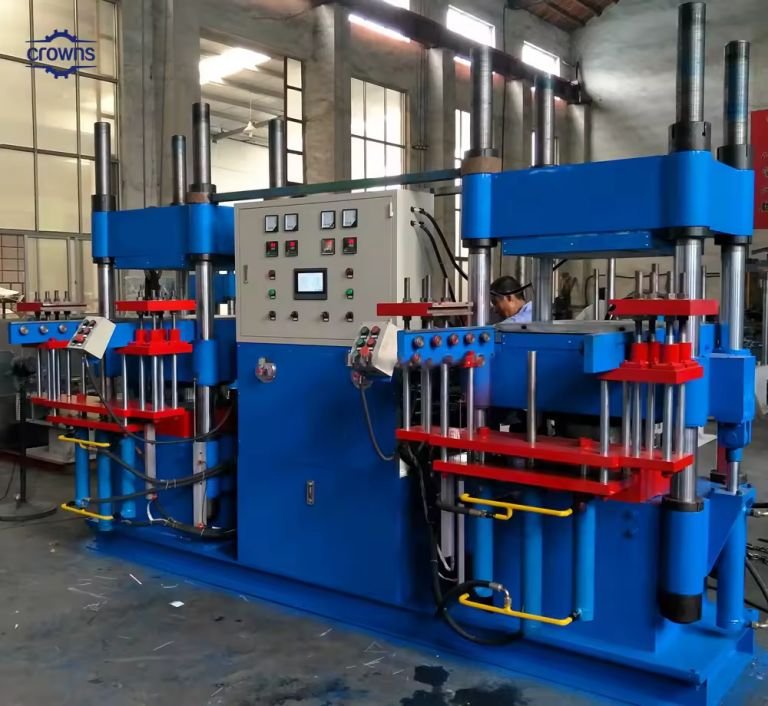
Table of Contents
Understanding Your Production Needs
Assessing Volume and Capacity
To choose the right rubber vulcanizing press, the first step is to evaluate your production volume. This involves understanding the quantity of rubber products you plan to produce within a given timeframe. More production will need bigger presses. They might also need more advanced automation to stay efficient.
Determine the required capacity based on your product output. Capacity refers to the amount of rubber the press can handle per cycle. For example, if you manufacture small rubber seals, a press with a lower capacity might suffice. However, for larger products like tires or parts, a larger press will be needed. It’s needed to meet production demands well.
Identifying Product Specifications
The next step is to identify the specific types of rubber products you will manufacture. Different products require different press specifications to ensure quality and efficiency. Consider the following factors:
Product Types: Identify whether you will be producing items like seals, gaskets, tires, or custom rubber components. Each type may require different mold sizes and configurations.
Dimensions: Measure the exact dimensions of your products. The size of the molds used in the press will need to match these dimensions to ensure proper shaping and curing.
Material Properties: Understand the specific material properties of the rubber you are using. This includes the rubber’s type (natural or synthetic), its hardness, and elasticity. It also includes any special additives that might affect vulcanization. Different rubbers require different temperature and pressure settings for optimal vulcanization.
By evaluating your production volume and identifying your product specs, you can choose a vulcanizing press. It will meet your needs and ensure high-quality output. At Crowns Machinery, we offer many customizable options. They match your unique production line needs. They ensure efficient and reliable manufacturing.
Types of Vulcanizing Presses
At Crowns Machinery, we offer a range of vulcanizing presses. These include Frame Plate, Conveyor Belt Hydraulic, and Column Rubber Vulcanizing Presses. Each is tailored to meet specific production needs. Our presses are known for their precision, durability, and reliability. They ensure efficient performance for various rubber manufacturing needs.
Frame Plate Vulcanizing Press
The Frame Plate Vulcanizing Press is a robust and versatile solution for producing a variety of rubber products. Its design ensures even pressure and temperature. This makes it ideal for high-precision jobs, such as seals, gaskets, and large industrial parts. The press is made of high-strength materials. It can withstand continuous operation, ensuring durability and consistent quality.
Conveyor Belt Hydraulic Press
The Conveyor Belt Hydraulic Press is engineered for the continuous production of conveyor belts. This press uses hydraulic pressure. It works with a conveyor system to automate vulcanization. This boosts production efficiency. It is great for high-volume manufacturing. It gives even vulcanization across the whole belt. This ensures high-quality, strong conveyor belts.
Column Rubber Vulcanizing Press
The press is for heavy-duty use. It needs high pressure and large molds. This press is ideal for manufacturing large rubber parts such as tires, bushings, and other industrial components. Its column-based structure provides great stability. It also ensures even pressure distribution. This keeps thick, heavy rubber products strong and high-quality.
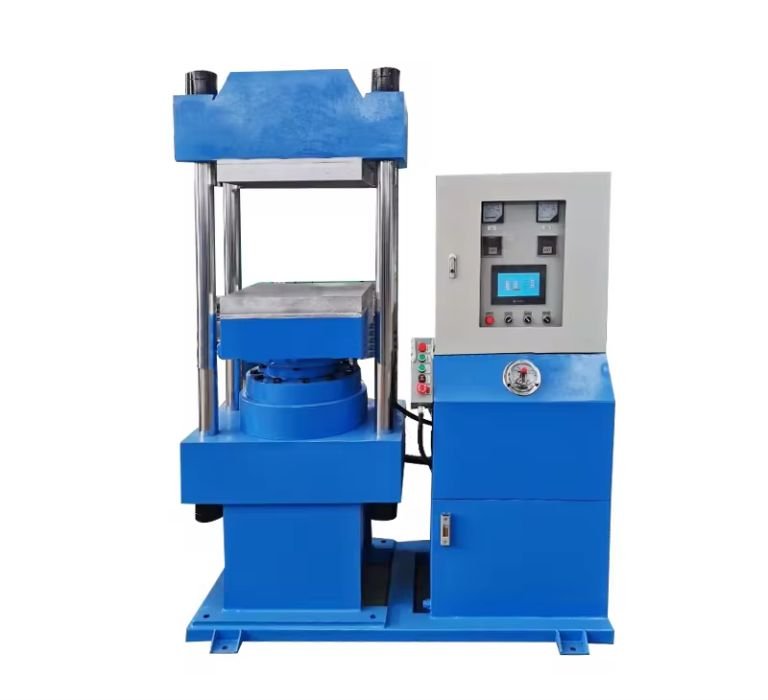
Key Features to Consider
When choosing a rubber vulcanizing press, you must consider customization options, build quality, materials, and tech advances. At Crowns Machinery, we offer durable presses. You can customize them to meet your needs. They have the latest technologies for top performance. These features make our vulcanizing presses reliable and efficient. They are a good solution for your rubber manufacturing needs.
Customization Options
Customization options are crucial for meeting specific production needs in rubber vulcanizing processes. Custom features allow businesses to tailor their presses to their needs. This enhances efficiency and product quality. At Crowns Machinery, we offer a wide range of customization options to ensure our vulcanizing presses meet diverse industrial needs.
For example, you can customize the mold sizes to fit different product sizes. This ensures precise shaping and vulcanization. You can integrate advanced systems for temperature and pressure control. They handle specific material properties. This improves the consistency and quality of the final product. You can also add more safety features. These include emergency stop buttons and protective enclosures. They make sure that operators are safe and that they follow industry standards. Custom automation features have automated loading and unloading. They can further streamline production. This cuts labor costs and raises throughput.
Build Quality and Materials
The build quality and materials used in a vulcanizing press significantly impact its durability and performance. The press uses high-quality materials. They let it withstand continuous use. This cuts how often it needs maintenance and repairs. At Crowns Machinery, we use top-grade materials such as stainless steel and hardened alloys to construct our presses. These materials resist wear and tear well. They last a long time even in tough production environments.
Vulcanizing presses use common materials. These include stainless steel for its corrosion resistance and strength. They also use cast iron for its durability and ability to withstand high pressures. They also use high-strength alloys that offer excellent wear resistance. We use these materials. They keep our presses reliable and high-performing over time. They are a solution for your rubber vulcanizing needs.
Technological Advancements
Advancements in vulcanizing presses offer many benefits. They improve efficiency, precision, and ease of use. At Crowns Machinery, we use advanced technologies. These include programmable logic controllers (PLCs) and automation systems. We use them to improve our presses for the vulcanization process.
PLCs allow for precise control over the vulcanization parameters, such as temperature, pressure, and timing. This level of control ensures consistent quality and reduces the likelihood of defects. Automation features can reduce labor costs. They can also increase production speed. They do this with automated loading and unloading. These systems can be programmed to handle complex vulcanization cycles. They ensure the best results with little manual work.
Also, you can add advanced monitoring and diagnostic systems. They provide real-time data on the press. This data can be used to make adjustments on the fly, further enhancing efficiency and product quality. It integrates with factory automation systems. This allows for seamless coordination with other production processes. It ensures a smooth and efficient workflow.
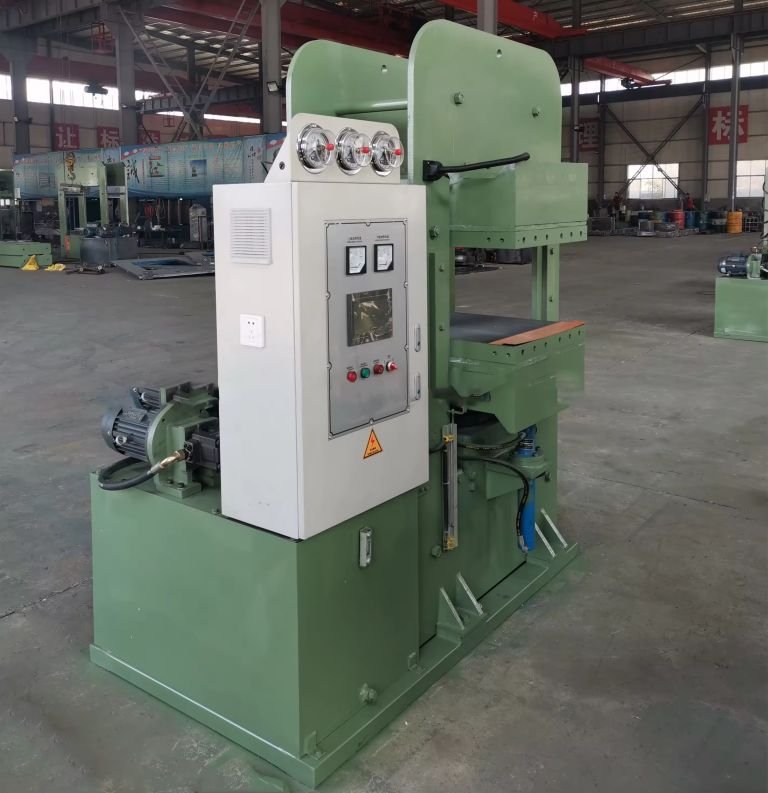
Evaluating Suppliers
Reputation and Experience
Choosing a reputable supplier is crucial when investing in a rubber vulcanizing press. A well-established supplier has a proven track record. They ensure that you receive high-quality equipment and reliable service. Reputation and experience show how well a supplier can meet standards and expectations in the industry. Crowns Machinery have years of experience in making and selling vulcanizing presses. Our extensive portfolio of satisfied customers reflects our commitment to quality and excellence. We have built a strong reputation by consistently delivering durable, efficient, and high-performance presses tailored to meet various industrial needs.
After-Sales Support
You need comprehensive after-sales support. It is essential for the long life and top performance of your vulcanizing press. This includes services such as installation, training, maintenance, and troubleshooting. At Crowns Machinery, we understand the importance of strong after-sales support. We offer many services to help our clients. Our support team is available to help with installation and setup, ensuring that your press is up and running smoothly from day one.
Success Story
X Rubber Company improved its production efficiency and product quality a lot. They did this by adding a rubber vulcanizing press from Crowns Machinery. Before this, X faced issues with inconsistent product quality and frequent downtime. They chose Crowns Machinery after much research. They picked us due to our strong reputation and ability to give custom solutions. The press has custom features. These include advanced temperature and pressure controls. They allowed X to do precise vulcanization. This resulted in high-quality products. The durable and reliable build of the press minimized downtime, enabling continuous and efficient production. X Rubber Company benefited from choosing Crowns Machinery. We provided tailored solutions that met their production needs. We also provided high-quality materials that ensured durability. And, they provided advanced technology that enhanced efficiency. This partnership shows how our commitment to quality and customer satisfaction can transform a company’s production process. It brings tangible benefits and big returns on investment.
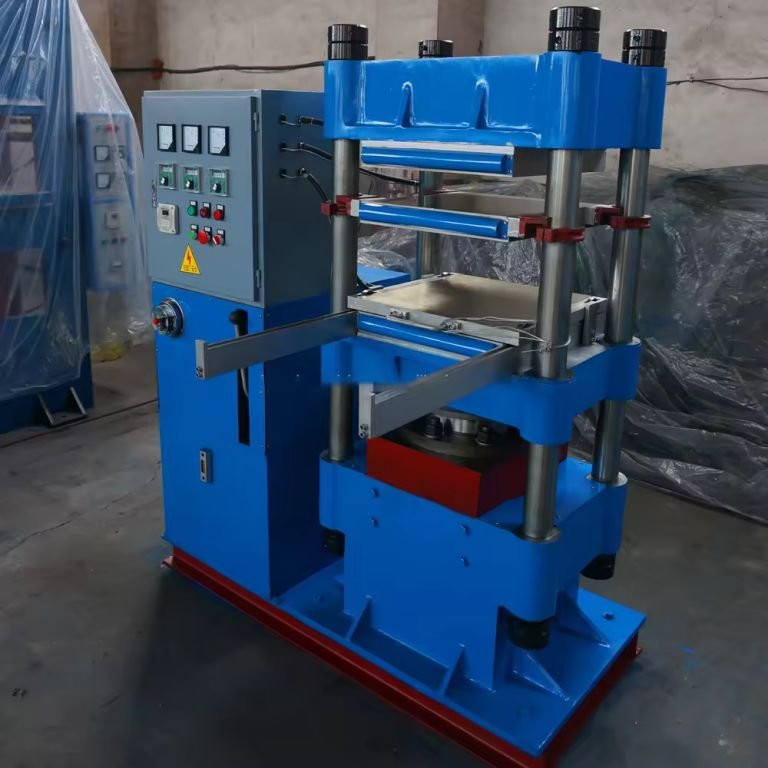
Conclusion
Selecting the right rubber vulcanizing press involves understanding your production needs, evaluating suppliers, and considering key features such as customization, build quality, and technological advancements. Crowns Machinery stands out by providing high-quality, cost-effective solutions tailored to diverse industrial requirements. For more information or to request a quote, contact Crowns Machinery today.
FAQ
The average production and delivery timeframe for a rubber vulcanizing press is typically 8 to 12 weeks. This period includes manufacturing, quality assurance checks, and shipping. Customizations may extend this timeframe slightly.
Yes, Crowns Machinery offers extensive customization options to meet your specific production needs. Customizations can include special mold sizes, precise temperature and pressure controls, automation features, and improved safety systems.
Crowns Machinery provides a comprehensive one-year warranty covering parts and labor. Additionally, we offer extra support. It includes regular maintenance and technical help. They ensure your press runs well over its lifespan.
Maintaining a rubber vulcanizing press involves regular inspections. You must lubricate moving parts and replace worn components on time. It is recommended to get monthly checks and annual maintenance. This will ensure the best performance and a long life.