Calendering is key in rubber production. It mixes raw rubber and shapes it into sheets or specific forms. These calendered rubber sheets are an important part of various industries due to their versatility.
Rubber sheets produced through calendering are used in various industries such as
Rubber Products Industry: Used in the manufacture of rubber flooring, rubber mats, etc.
Tyre manufacturing industry: essential for the manufacture of tire treads and sidewalls.
Seal Manufacturing: Essential for the production of a wide range of seals, gaskets, and other sealing products.
Understanding the thickness of calendered rubber is critical to these industries. It directly affects the quality, durability, and performance of the final product. In the next pages, Crowns Machinery will show you how to control the thickness of a rubber sheet. It will cover how to measure it and what it means to adjust it for different uses.
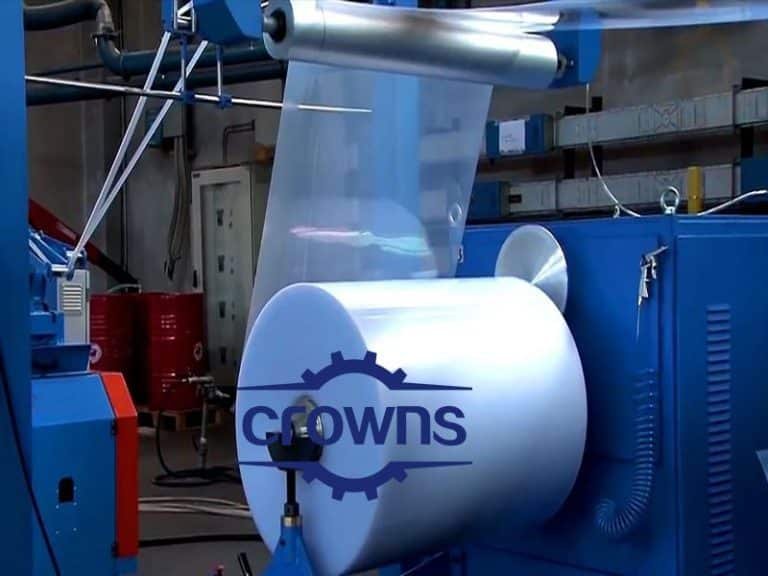
Table of Contents
Rubber Calender and Rubber Sheet
Rubber calender: A rubber calender is a specialized equipment used for mixing and processing rubber. It consists of two parallel rollers that work by extruding and stretching the rubber. This process shapes the rubber into sheets or other required forms with varying thicknesses. The rollers can be precisely controlled. This allows for making rubber sheets to meet specific thickness requirements. These requirements are essential for different applications.
Rubber sheet: A rubber sheet is a product created by the rubber calendar. The thickness of these sheets is critical as it directly determines whether the rubber sheet meets the needs of its intended industry. For example, the electronics industry needs thin sheets. But, the automotive and industrial sectors need thick ones.
Methods of adjusting and controlling the thickness of rubber sheet by calender machine
Adjust the roller spacing: The operator can control the rubber sheet’s thickness by adjusting the calender’s roller spacing. Smaller spacing means less thickness. Larger spacing means more thickness.
Improve the flatness of the roller surface: The roller’s flatness affects the rubber sheet’s smoothness. This, in turn, affects the sheet’s thickness.
Control the temperature of the rollers: Roller problems can affect rubber flow. But, controlling the roller temperature can make it more uniform. This achieves uniform and consistent thickness.
Adjust the feed speed: Faster feed makes thinner rubber. So, by controlling feed, you can control thickness.
Thickness range
Rubber sheets are widely used in many industries. Their thickness varies from thin to thick.
Thin sheet: The thickness is usually 0.1-1mm. It is mainly used to make thin seals for electronics, medical equipment, and so on.
Medium thickness flakes: It is usually 1mm-5mm thick. It is mainly used in car parts, pipes, and mechanical seals.
Thicker sheet: The thickness is usually over 5mm. It mainly supports and buffers the rubber structure of the gaskets.
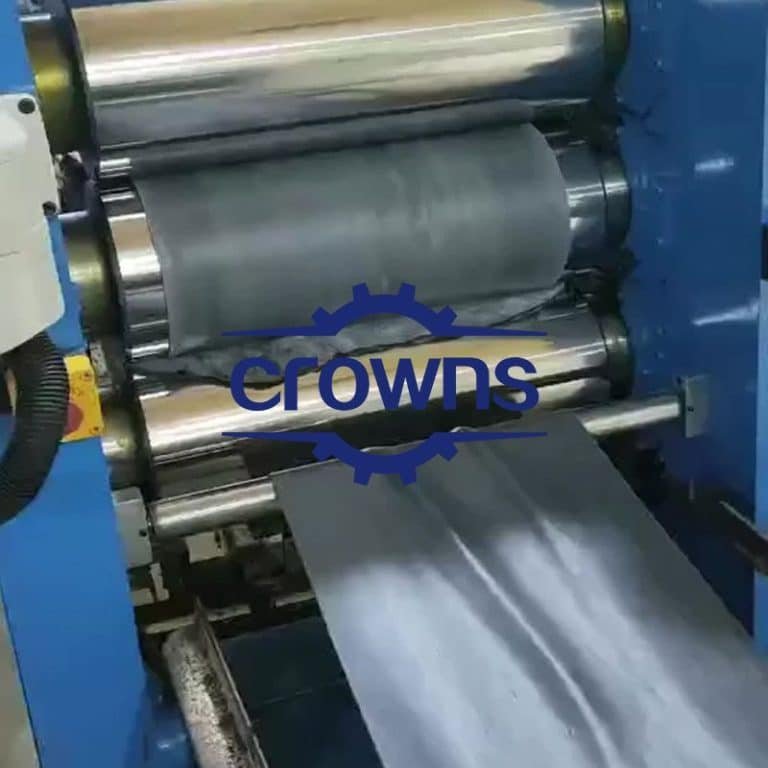
Thickness measurement and control technology
Laser Measurement: We measure the light beam emitted by the laser on the rubber sheet’s surface. We do this to calculate its thickness. The measurement method is highly accurate and suitable for thin flakes. It is mainly used in industries. These industries include medical devices and electronics. They require high precision.
Infrared Measurement: We use the rubber sheet to absorb infrared rays. The rays have specific absorption traits. We measure the infrared reflection to find the sheet’s thickness. It can measure transparent or semi-transparent materials. It can also measure rubber sheets in rubber production.
Ultrasonic measurement: We calculate the thickness of a rubber sheet by measuring the time it takes for ultrasonic waves to pass through it. Non-contact measurement is used for some special environments. These include high temperature or corrosion. It is used to measure the thickness of medium or thick rubber sheets.
Importance of rubber sheet thickness
The thickness of a rubber sheet is key. It affects its durability, safety, and other key properties. The importance of rubber sheet thickness in different applications is analyzed below:
Sealing material: The rubber sheet’s thickness directly affects its sealing. Being too thin or too thick hurts the material’s adaptability. Only the right thickness can ensure the reliability of its seal. It keeps leaks of liquid or gas in various conditions.
Conveyor belt: The rubber sheet’s thickness affects the conveyor belt. It affects its strength and flexibility. These things affect the belt’s service life and its load capacity. Only the right thickness can keep it stable. It must stay stable in different workplaces.
Vibration pads: The rubber sheet’s thickness affects the vibration pad’s shock absorption. It also affects its buffer effect. Only the right thickness ensures that it absorbs energy and dampens vibrations. It never improves equipment stability.
Customised thickness requirements
In some industries, rubber sheet thickness must be customized. The rubber calendar can be adjusted by changing the roller spacing, temperature, pressure, and other parameters. This lets it work with different materials, thicknesses, and production needs. So, it can be very flexible and meet many rubber sheet thickness requirements.
Automotive industry: To seal well and damp vibrations, rubber sheets must be thick. They need to be customized.
Electronic products industry: Seals and dust pads used in electronics need very thin rubber sheets. So, they need to be customized.
Medical device industry: Rubber sheets in this industry need to resist chemicals and seal well. So, their thickness must be tailored.
Conclusion
Crowns Machinery understands that many things affect rubber sheet thickness. These include sealing, strength, vibration damping, and cushioning. They also include the needs of different industries.
Our advanced rubber calenders are designed to adjust thickness precisely. They do this through techniques like changing roll spacing, pressure, and temperature. We also incorporate state-of-the-art measurement methods including laser, infrared, and ultrasonic technologies.
By considering these factors and employing our cutting-edge equipment and methods, we ensure the production of rubber sheets that meet the highest industry standards and specific application requirements. At Crowns Machinery, we provide the solutions you need to produce high-quality rubber sheets that satisfy the diverse demands of many industries.