Conventional Calendered Vs. Non-Calendered Tyre Manufacturing-Conventional calendering is a common tyre manufacturing method. In this method, the rubber mix is processed through a series of calenders and extruders. The method forms the various components of a tyre, such as the tread, the cord, the sidewalls, and so on. These components are then combined to form the overall structure of the tyre.
In non-calendered tyre manufacturing, the rubber mix is sprayed or coated directly into the tyre mould. Various techniques, such as vibration or electromagnetic fields, are then used to distribute the rubber uniformly in the mould and form the tyre’s components.
The choice of manufacturing method depends on the specific needs of production, the level of technology, and economic factors.
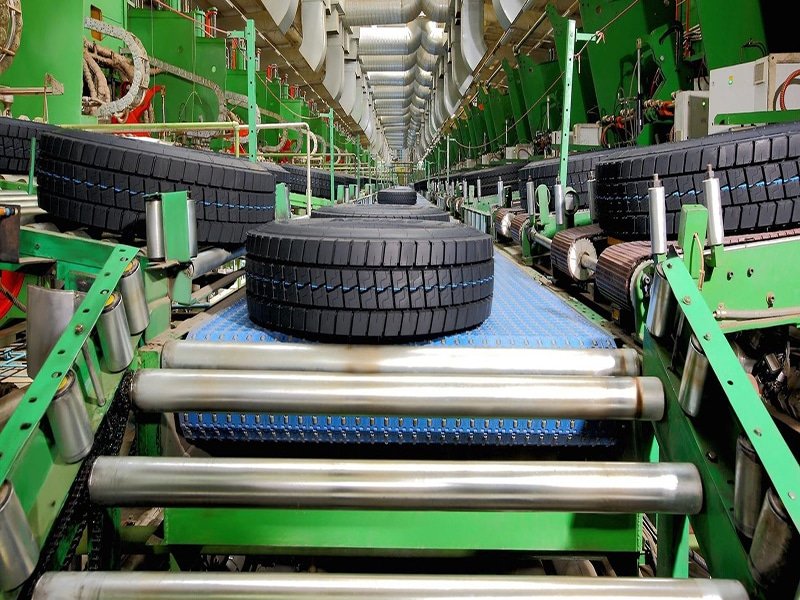
Table of Contents
Traditional calendered tyre manufacturing process
1) Rubber mixing: Raw materials, like natural rubber and synthetic rubber, are mixed with fillers, reinforcing materials, vulcanising agents, etc. This forms a homogeneous rubber compound.
2) Cord preparation: Cord fabrics of materials such as nylon or polyester are coated into the rubber to form a cord with a rubber cover. These cord fabrics act as reinforcement and support in the tyre.
3) Embryo Manufacturing: The embryo is the main structure of the tyre and consists of the sidewalls and the tread. Cut and assemble the rubber-covered cord fabric to shape and structure the embryo.
4) Calendering: A series of calendering machinery and equipment shapes the embryo into the required shape. It ensures that the various parts are homogenous and consistent.
5) Forming: The calendered embryo is placed in a forming machine. It is heated and cooled to give the tire its final shape.
The traditional calendered tyre manufacturing process ensures relatively consistent product quality at relatively low cost. However, it has limitations, such as high energy consumption, long mould change times, a time-consuming production process, and a certain environmental impact.
The rise of calenderless tyre manufacturing technology
In recent years, the tyre manufacturing sector has been engaged in technological innovation and research and development. They aim to improve tyre performance, reduce costs, and lessen environmental impact. New materials have been introduced, manufacturing processes have improved, and production has become more automated. All of these changes have contributed to the emergence of new technologies.
Continuous innovation in advanced rubber coating technology and other new manufacturing processes has contributed to the development of calenderless tyre manufacturing technology. These new technologies allow for more precise control of rubber distribution during the tyre manufacturing process. They improve productivity and tyre quality.
Therefore, the rise of calenderless tyre manufacturing is the result of a combination of factors. It reflects the manufacturing industry’s ability to innovate and adapt in the face of market challenges.

Material selection and performance differences
Traditional calendered tyre manufacturing
- Its materials usually use natural rubber, synthetic rubber filler, the cord fabric can be nylon, polyester and so on.
- During the manufacturing process, tyre performance is easily affected by internal stresses.
Non-calendered tyre manufacturing
- Rubber is sprayed directly onto the mould with a variety of rubber types. The cord fabric is still needed, but its adhesion may be more critical in the spraying process.
- The manufacturing process improves the tire’s durability. It avoids the calendering process and reduces internal stresses.
Production efficiency and cost comparison
Calendered tyre manufacturing
- Traditional calendered tyre manufacturing usually requires long lead times. This is because of the multiple steps involved.
- The cost of calendering machinery and moulding equipment is relatively high, and energy consumption is also higher for large equipment.
Uncalendered tyre manufacturing
- Uncalendered tyre manufacturing is generally more flexible. It involves fewer process steps, which allows for greater productivity and faster changeover from one type of tyre to another.
Large calendering machines aren’t needed, so energy consumption is lower. New technologies, such as rubber coating, although costly, are relatively flexible. They also allow for shorter mould changes and less production line standstill time.
Quality control and safety standards
Calendered tyre manufacturing
- The calendered tyre manufacturing process complies with traditional tyre manufacturing standards. Those standards have been widely accepted and used in the manufacturing industry.
- The traditional calendered tyre manufacturing process requires strict monitoring to meet quality standards. This includes monitoring calendering, moulding, curing, and running complex tests for appearance and size.
- The traditional calendered tyre manufacturing process requires a series of durability and other performance tests. These tests ensure that the tyre is safe and reliable under various conditions.
Calenderless tyre manufacturing
- The key to non-calendered tyre manufacturing is the need for more precise control of the rubber spraying process to ensure the uniform distribution of rubber. Additionally, using digital technology for real-time monitoring of the production process improves the consistency of production and product quality.
- The tire manufacturing process does not use a calender, which makes the tires more durable. This improves car safety because the tires have better performance.
Environmental protection and sustainable development
Compared with the traditional calendered tyre manufacturing process, the calenderless tyre manufacturing process does not involve large calendering machinery and equipment, the production process does not produce excessive waste and energy consumption, and has a small impact on the environment, so it is more in line with the manufacturing industry’s pursuit of sustainable development and environmental protection.
Conclusion
Because of the calendered tyre manufacturing compared to traditional calendered tyre manufacturing in the production efficiency, cost, tyre performance, environmental protection and other aspects of the existence of certain advantages of the difference, to the industry has brought a series of positive changes, promoting the tyre manufacturing industry to more efficient, more flexible and more environmentally friendly direction, more in line with the industry’s general direction of the development of the needs of the industry.
For those seeking to explore advanced tire manufacturing solutions, professional advice can be gained by partnering with a company such as Crowns Machinery, which specializes in the manufacture and sale of rubber calenders, and we will provide state-of-the-art machinery and expertise.